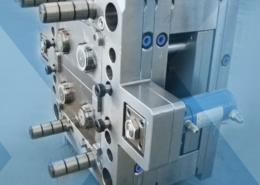
Unveiling the Potential of Polyethylene Injection Molding: Transforming Manufact
Author:gly Date: 2024-06-08
Introduction
Polyethylene injection molding stands as a cornerstone of modern manufacturing, offering versatility, efficiency, and cost-effectiveness in the production of a wide range of plastic components. In this article, we delve into the intricacies of polyethylene injection molding, exploring its applications, advantages, and future prospects, igniting readers' curiosity about its transformative capabilities.
Understanding Polyethylene Injection Molding
The Basics
Polyethylene injection molding involves the melting of polyethylene resin pellets and injecting the molten material into a mold cavity, where it solidifies to form the desired component. This process is facilitated by injection molding machines equipped with precision control systems for temperature, pressure, and cooling.
Types of Polyethylene
Polyethylene is available in various grades and types, each with distinct properties suited for specific applications. High-density polyethylene (HDPE), low-density polyethylene (LDPE), and linear low-density polyethylene (LLDPE) are among the most commonly used types in injection molding, offering different levels of strength, flexibility, and chemical resistance.
Advantages of Polyethylene Injection Molding
Polyethylene injection molding offers numerous advantages over alternative manufacturing methods:
- Versatility: Polyethylene can be molded into complex shapes with high precision, making it suitable for a wide range of applications across industries.
- Cost-effectiveness: Injection molding allows for high-volume production at low per-unit costs, making it economically viable for mass production.
- Durability: Polyethylene components exhibit excellent durability and resistance to corrosion, chemicals, and environmental factors, ensuring long-lasting performance.
- Recyclability: Polyethylene is recyclable, contributing to sustainability efforts and reducing environmental impact.
Applications of Polyethylene Injection Molding
Packaging
Polyethylene injection molding is widely used in the packaging industry for the production of bottles, containers, caps, and closures. Its lightweight, durable, and customizable nature makes it ideal for packaging solutions across various sectors, including food and beverage, pharmaceuticals, and cosmetics.
Automotive Components
In the automotive industry, polyethylene injection molding is employed for the manufacturing of interior and exterior components such as dashboards, bumpers, and trim panels. Its ability to withstand extreme temperatures, impact, and harsh chemicals makes it a preferred choice for automotive applications.
Consumer Goods
Consumer goods ranging from household appliances to toys and sporting goods utilize polyethylene injection molding for the fabrication of parts and components. Its versatility, cost-effectiveness, and aesthetic appeal make it a popular choice among manufacturers seeking to meet consumer demand for innovative products.
Future Prospects and Recommendations
The future of polyethylene injection molding holds immense promise, with ongoing advancements in materials, technology, and sustainability paving the way for new opportunities. To harness its full potential, continued research and development efforts should focus on:
Enhancing Material Properties
: Further refinement of polyethylene formulations to improve mechanical strength, heat resistance, and recyclability.
Advanced Manufacturing Techniques
: Integration of additive manufacturing and digital design tools to optimize production processes and reduce time-to-market.
Sustainability Initiatives
: Adoption of sustainable practices such as biodegradable polymers, closed-loop recycling systems, and renewable energy sources to minimize environmental impact.
Conclusion
In conclusion, polyethylene injection molding emerges as a game-changer in the realm of manufacturing, offering unmatched versatility, efficiency, and sustainability. By understanding its mechanisms, applications, and future prospects, businesses can unlock new avenues for innovation and growth. As we embark on the journey towards a more sustainable and technologically advanced future, polyethylene injection molding stands poised to lead the way, transforming industries and shaping the world of tomorrow.
GETTING A QUOTE WITH LK-MOULD IS FREE AND SIMPLE.
FIND MORE OF OUR SERVICES:
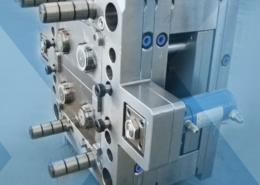
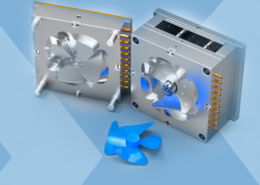
Plastic Molding
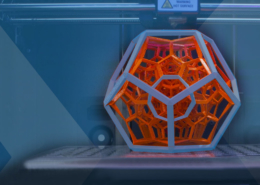
Rapid Prototyping
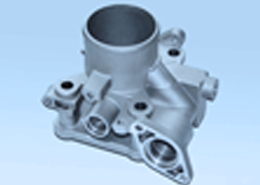
Pressure Die Casting
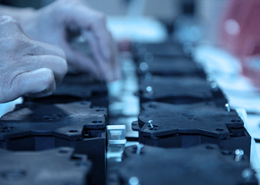
Parts Assembly
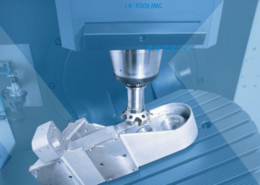