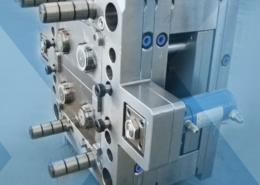
Exploring POM Injection Molding: Precision Engineering for Enhanced Performance
Author:gly Date: 2024-06-08
Introduction:
POM (Polyoxymethylene), commonly known as acetal or Delrin, is a versatile engineering thermoplastic renowned for its exceptional strength, stiffness, and dimensional stability. POM injection molding, the process of injecting molten POM resin into a mold cavity to produce precise components, has revolutionized industries ranging from automotive to electronics. This article delves into the world of POM injection molding, exploring its applications, advantages, challenges, and future prospects.
Understanding POM Injection Molding
POM injection molding is a highly specialized manufacturing process that involves injecting molten POM resin into a pre-designed mold cavity under high pressure and temperature. This process allows for the production of intricate parts with tight tolerances and excellent surface finishes. POM's unique properties, including low friction, chemical resistance, and thermal stability, make it an ideal choice for applications requiring high precision and durability.
Applications Across Industries
The versatility of POM injection molding enables its use in a wide range of industries, including automotive, electronics, aerospace, and consumer goods. In the automotive sector, POM components such as gears, bearings, and fuel system parts contribute to improved performance, efficiency, and longevity of vehicles. Similarly, in the electronics industry, POM is used in connectors, switches, and housings due to its electrical insulating properties and dimensional stability.
Advantages and Challenges
POM injection molding offers several advantages, including high strength-to-weight ratio, chemical resistance, low friction, and excellent machinability. Additionally, POM's ability to maintain dimensional stability over a wide temperature range makes it suitable for demanding applications. However, challenges such as moisture absorption, shrinkage, and warpage during molding require careful consideration and process optimization to ensure optimal results.
Technological Innovations and Future Trends
Advancements in POM injection molding technology continue to drive innovation and efficiency in manufacturing processes. From the development of advanced mold designs to the integration of real-time monitoring and control systems, manufacturers are constantly pushing the boundaries of what's possible with POM injection molding. Future trends may include the adoption of sustainable materials, such as bio-based POM resins, and the implementation of additive manufacturing techniques for rapid prototyping and customization.
Conclusion
In conclusion, POM injection molding represents a cornerstone of modern manufacturing, offering unparalleled precision, performance, and versatility across diverse industries. By understanding the fundamentals of POM injection molding, stakeholders can harness its potential to innovate and excel in their respective fields. Looking ahead, continued research and development, coupled with advancements in technology and materials science, will further enhance the capabilities and applications of POM injection molding, driving progress and innovation in the years to come.
GETTING A QUOTE WITH LK-MOULD IS FREE AND SIMPLE.
FIND MORE OF OUR SERVICES:
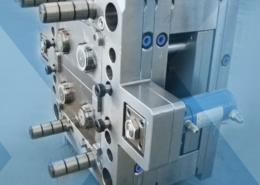
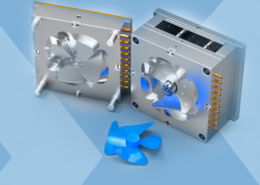
Plastic Molding
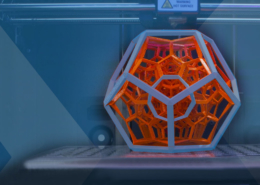
Rapid Prototyping
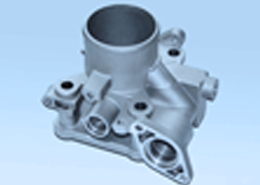
Pressure Die Casting
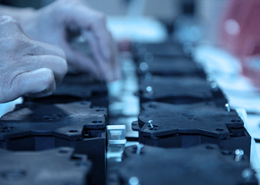
Parts Assembly
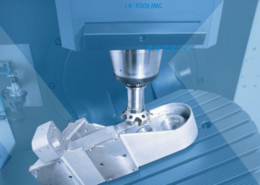