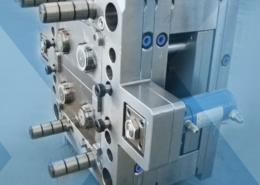
Exploring the Marvels of PP Injection
Author:gly Date: 2024-06-08
PP injection, a fascinating process in the realm of polymer engineering, has captured the attention of researchers, engineers, and enthusiasts alike. In this article, we delve into the intricacies of PP injection, unraveling its significance, applications, and future prospects.
Introduction to PP Injection
Polypropylene (PP) injection molding stands as a cornerstone in the domain of plastic manufacturing. It involves the transformation of polypropylene pellets into complex shapes through the application of heat and pressure. This process has revolutionized various industries, ranging from automotive and consumer goods to medical devices and packaging.
Properties of PP
Polypropylene exhibits a myriad of advantageous properties, making it an ideal candidate for injection molding. Its high tensile strength, chemical resistance, and thermal stability render it suitable for diverse applications. Moreover, PP's lightweight nature and cost-effectiveness further contribute to its widespread usage in the manufacturing sector.
Process Overview
The PP injection molding process encompasses several distinct stages, each playing a crucial role in ensuring the production of high-quality parts. From material preparation and injection to cooling and ejection, meticulous attention to detail is imperative to achieve optimal results. Advanced machinery and precise control parameters facilitate the seamless execution of each step, guaranteeing efficiency and consistency in production.
Applications Across Industries
The versatility of PP injection molding transcends boundaries, finding application in a plethora of industries. In the automotive sector, PP components contribute to lightweighting efforts, enhancing fuel efficiency and performance. Similarly, in the medical field, PP-based devices uphold stringent regulatory standards while delivering exceptional performance and reliability. Additionally, the consumer goods industry harnesses PP injection molding to craft intricate designs and functional products that resonate with modern consumers.
Challenges and Innovations
Despite its widespread adoption, PP injection molding encounters certain challenges, ranging from warpage and shrinkage to environmental concerns regarding plastic waste. However, ongoing research and technological advancements continue to address these issues. Novel approaches such as additive manufacturing and biodegradable polymers offer promising solutions, paving the way for a more sustainable future.
Quality Assurance and Optimization
Maintaining stringent quality standards is paramount in PP injection molding to uphold product integrity and customer satisfaction. Through meticulous process optimization and rigorous quality control measures, manufacturers strive to minimize defects and enhance efficiency. Advanced analytics and machine learning algorithms enable real-time monitoring and predictive maintenance, ensuring seamless operations and minimal downtime.
Environmental Considerations
In an era marked by growing environmental consciousness, the sustainability of PP injection molding emerges as a pressing concern. Efforts to reduce carbon footprint and embrace circular economy principles drive the adoption of recycled materials and eco-friendly practices. Additionally, the development of bio-based polymers holds immense potential in mitigating environmental impact while maintaining performance standards.
Conclusion
In conclusion, PP injection molding stands as a testament to human ingenuity and innovation, revolutionizing the manufacturing landscape across industries. From its remarkable properties to diverse applications and ongoing advancements, the significance of PP injection molding is undeniable. Embracing sustainability and continuous improvement, we embark on a journey towards a future where PP injection molding thrives as a pillar of modern manufacturing.
Through collaborative research and interdisciplinary efforts, we can unlock new possibilities and usher in an era of unprecedented innovation in polymer engineering. As we navigate the complexities of the modern world, let us harness the transformative power of PP injection molding to create a sustainable and prosperous future for generations to come.
GETTING A QUOTE WITH LK-MOULD IS FREE AND SIMPLE.
FIND MORE OF OUR SERVICES:
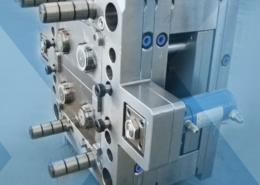
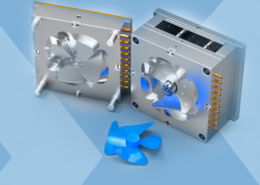
Plastic Molding
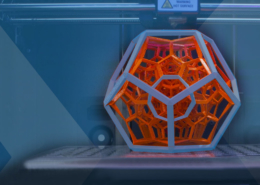
Rapid Prototyping
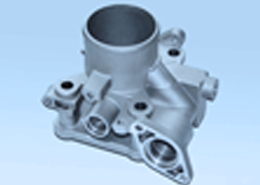
Pressure Die Casting
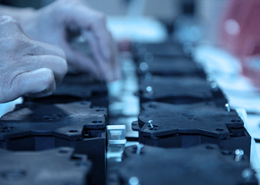
Parts Assembly
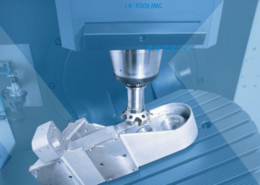