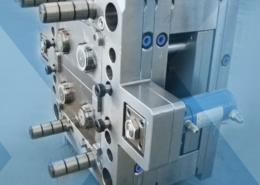
Unraveling the Potential of PP Moulding: Enhancing Manufacturing Efficiency and
Author:gly Date: 2024-06-08
Introduction:
PP (Polypropylene) moulding stands at the forefront of modern manufacturing, offering a versatile and cost-effective solution for producing a wide range of plastic products. With its unique combination of properties, including strength, flexibility, and chemical resistance, PP has become a preferred choice for various industries. This article explores the world of PP moulding, delving into its applications, benefits, challenges, and future prospects.
Understanding PP Moulding
PP moulding involves the injection of molten polypropylene resin into a mould cavity, where it solidifies to form a desired shape. This process allows for the production of intricate components with high precision and consistency. PP's excellent flow characteristics and ability to maintain dimensional stability make it well-suited for a wide range of applications, from packaging to automotive components.
Applications Across Industries
The versatility of PP moulding makes it indispensable across various industries, including automotive, consumer goods, healthcare, and packaging. In the automotive sector, PP is used for manufacturing interior trim components, exterior body panels, and under-the-hood parts due to its lightweight, impact resistance, and durability. Similarly, in the consumer goods industry, PP moulding is employed for producing household items, toys, and electronic enclosures.
Advantages and Challenges
PP moulding offers several advantages, including low cost, ease of processing, recyclability, and resistance to chemicals and moisture. Additionally, PP's high strength-to-weight ratio and excellent thermal properties make it a preferred choice for applications requiring durability and stability. However, challenges such as shrinkage, warpage, and surface defects during moulding require careful process optimization and mold design to ensure optimal results.
Technological Innovations and Future Trends
Advancements in PP moulding technology continue to drive innovation and efficiency in manufacturing processes. From the development of advanced mold designs to the integration of automation and robotics, manufacturers are constantly striving to improve productivity and quality in PP moulding operations. Future trends may include the adoption of sustainable materials, such as bio-based PP resins, and the implementation of digital manufacturing techniques for real-time monitoring and optimization.
Conclusion
In conclusion, PP moulding represents a cornerstone of modern manufacturing, offering unparalleled versatility, efficiency, and sustainability across diverse industries. By understanding the fundamentals of PP moulding and embracing technological advancements, stakeholders can harness its potential to innovate and excel in their respective fields. Looking ahead, continued research and development, coupled with collaboration and adoption of sustainable practices, will further enhance the capabilities and applications of PP moulding, driving progress and innovation in the years to come.
GETTING A QUOTE WITH LK-MOULD IS FREE AND SIMPLE.
FIND MORE OF OUR SERVICES:
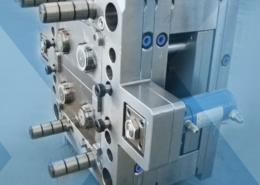
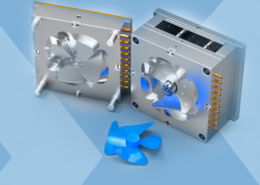
Plastic Molding
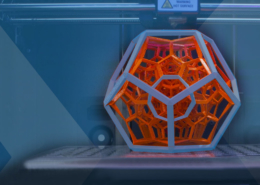
Rapid Prototyping
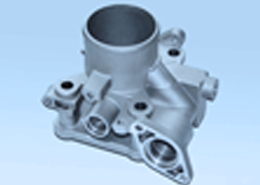
Pressure Die Casting
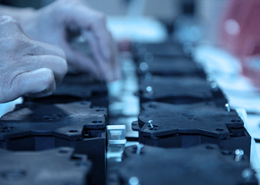
Parts Assembly
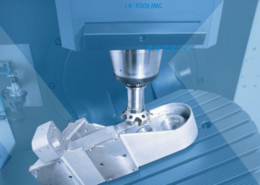