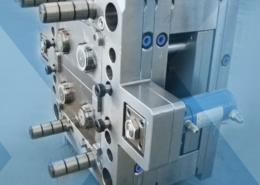
Exploring the World of Prototyping and Plastic Molds
Author:gly Date: 2024-06-08
In the realm of manufacturing and product development, the processes of prototyping and plastic molding stand as crucial pillars, shaping the way products are conceptualized, refined, and ultimately brought to life. From the inception of an idea to the mass production of a finished product, the journey often begins with the creation of a prototype and the utilization of plastic molds. This article delves into the intricacies of these processes, shedding light on their significance, methodologies, and impact on various industries.
The Essence of Prototyping
Prototyping serves as a fundamental stage in the product development cycle, offering designers and engineers a tangible representation of their concepts. By creating prototypes, developers can evaluate the functionality, aesthetics, and feasibility of their designs before committing to large-scale production. This iterative approach allows for adjustments and refinements, ultimately leading to the development of superior products.
Understanding Prototyping Methods
Prototyping encompasses various techniques, ranging from simple handcrafted models to advanced computer-aided designs (CAD) and additive manufacturing processes like 3D printing. Each method offers unique advantages and limitations, catering to the specific needs of different projects. While traditional prototyping methods provide a hands-on approach for visualizing designs, modern technologies enable rapid prototyping with enhanced precision and efficiency.
The Role of Prototyping in Innovation
Innovation thrives on experimentation and iteration, and prototyping serves as a catalyst for this process. By facilitating quick iterations and feedback loops, prototypes empower innovators to explore new ideas, push boundaries, and uncover unforeseen opportunities. Whether in the development of groundbreaking technologies or the enhancement of existing products, prototyping fuels the engine of innovation, driving progress and evolution across industries.
Unveiling the Power of Plastic Molds
Plastic molding stands as a cornerstone of modern manufacturing, revolutionizing the production of a wide range of products, from consumer goods to automotive components. This transformative process harnesses the versatility and cost-effectiveness of plastics, enabling the mass production of intricate shapes and designs with remarkable efficiency.
The Anatomy of Plastic Molding
At its core, plastic molding involves the shaping of molten plastic material into a desired form using a mold. This mold, typically made from metal, serves as a negative impression of the final product, allowing for precise replication at scale. Through techniques such as injection molding, blow molding, and rotational molding, manufacturers can achieve high levels of detail and consistency, meeting the diverse needs of consumers worldwide.
Advancements in Plastic Molding Technology
The field of plastic molding has witnessed significant advancements in recent years, driven by innovations in materials, machinery, and process optimization. Advanced polymers, nanocomposites, and bio-based resins offer improved performance characteristics and sustainability, opening new possibilities for product design and development. Moreover, the integration of automation, robotics, and artificial intelligence has enhanced the precision, speed, and efficiency of plastic molding operations, driving productivity and competitiveness in the global market.
Convergence of Prototyping and Plastic Molding
In the interconnected landscape of product development, the synergy between prototyping and plastic molding is undeniable. These complementary processes work in tandem to streamline the journey from concept to commercialization, offering manufacturers a seamless pathway to innovation and success.
Prototyping for Mold Design and Validation
Prototyping plays a crucial role in the design and validation of plastic molds, providing insights into factors such as part geometry, material compatibility, and mold functionality. By creating prototypes for mold testing and iteration, designers can identify potential issues early in the development cycle, minimizing costly revisions and production delays. This collaborative approach ensures the alignment of design intent with manufacturing feasibility, paving the way for efficient mold production and optimization.
Leveraging Rapid Prototyping in Mold Manufacturing
The emergence of rapid prototyping technologies has revolutionized the landscape of mold manufacturing, enabling designers to iterate quickly and cost-effectively. Techniques such as stereolithography (SLA), selective laser sintering (SLS), and fused deposition modeling (FDM) empower mold makers to create intricate prototypes with unprecedented speed and accuracy. By leveraging these advanced prototyping methods, manufacturers can accelerate the development cycle, reduce time-to-market, and gain a competitive edge in the dynamic business environment.
Conclusion: Shaping the Future of Manufacturing
In conclusion, the realms of prototyping and plastic molding converge to form the backbone of modern manufacturing, driving innovation, efficiency, and quality across industries. By embracing the iterative nature of prototyping and the transformative potential of plastic molding, businesses can navigate the complexities of product development with confidence and agility. As technology continues to advance and boundaries are pushed, the synergy between prototyping and plastic molding will continue to shape the future of manufacturing, unlocking new possibilities and propelling progress towards a more sustainable and prosperous world.
GETTING A QUOTE WITH LK-MOULD IS FREE AND SIMPLE.
FIND MORE OF OUR SERVICES:
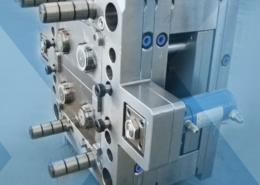
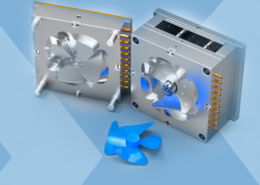
Plastic Molding
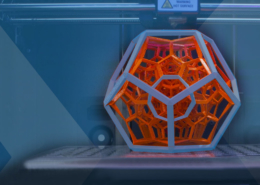
Rapid Prototyping
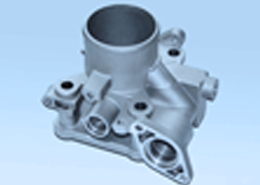
Pressure Die Casting
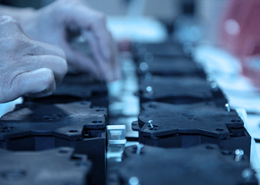
Parts Assembly
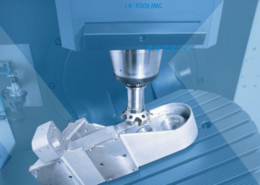