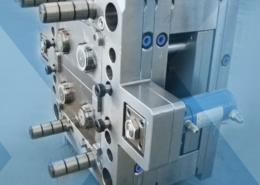
Unveiling the World of Prototype Injection
Author:gly Date: 2024-06-08
In the realm of product development, speed and precision are paramount. Prototype injection molding stands as a beacon of innovation in this regard. This article delves into the intricacies of prototype injection molding, its applications, advantages, challenges, and future prospects, aiming to captivate readers with its significance and potential.
Introduction
Prototype injection molding serves as a cornerstone in the product development lifecycle, enabling engineers and designers to transform concepts into tangible prototypes quickly and cost-effectively. This iterative process allows for design validation, functional testing, and market evaluation, accelerating time-to-market and fostering innovation.
Versatility and Flexibility
Adaptable Solutions
Prototype injection molding offers unparalleled versatility, accommodating a wide range of materials, geometries, and complexities. From simple single-cavity molds to complex multi-cavity configurations, the process caters to diverse prototyping needs across industries, including automotive, medical, consumer electronics, and aerospace.
Rapid Iteration
The iterative nature of prototype injection molding enables rapid design iterations and modifications. With short lead times and low setup costs, designers can quickly refine prototypes based on feedback, iterate on multiple design iterations simultaneously, and expedite the product development cycle.
Precision Engineering
Tight Tolerances
Precision is paramount in prototype injection molding. Advanced mold design and manufacturing techniques, coupled with state-of-the-art injection molding machines, ensure tight tolerances and dimensional accuracy, allowing for the creation of prototypes that closely mimic final production parts.
Complex Geometries
Prototype injection molding empowers designers to explore complex geometries and intricate features that are challenging or impossible to achieve through traditional manufacturing methods. From undercuts and thin walls to intricate surface textures, the process unlocks endless possibilities for creative design expression.
Cost-Efficiency and Risk Mitigation
Cost-Effective Prototyping
Prototype injection molding offers a cost-effective alternative to traditional prototyping methods such as CNC machining and 3D printing, especially for medium to high-volume production runs. By leveraging economies of scale and amortizing tooling costs over multiple parts, the per-unit cost of prototypes is significantly reduced.
Risk Mitigation
Prototype injection molding mitigates risks associated with product development by providing tangible prototypes for comprehensive testing and evaluation. Identifying design flaws, functionality issues, and manufacturing challenges early in the development process minimizes costly revisions and rework during later stages.
Challenges and Future Directions
Material Selection
Choosing the right material is critical in prototype injection molding. While a wide range of engineering-grade thermoplastics and elastomers are available, the selection process requires careful consideration of material properties, performance requirements, and cost constraints to ensure optimal prototype quality and functionality.
Process Optimization
Optimizing the injection molding process for prototype production presents unique challenges. Balancing speed, quality, and cost-effectiveness requires fine-tuning process parameters, optimizing tooling designs, and implementing advanced process monitoring and control systems to achieve consistent and reliable results.
Conclusion
In conclusion, prototype injection molding serves as a cornerstone in the product development lifecycle, enabling rapid iteration, precision engineering, and cost-effective prototyping. Its versatility, flexibility, and ability to mitigate risks empower designers and engineers to accelerate innovation, reduce time-to-market, and bring products to market faster and more efficiently. As technology continues to evolve and market demands evolve, the future of prototype injection molding holds promise for further advancements in material science, process optimization, and integration with emerging technologies, shaping the landscape of product development for years to come.
GETTING A QUOTE WITH LK-MOULD IS FREE AND SIMPLE.
FIND MORE OF OUR SERVICES:
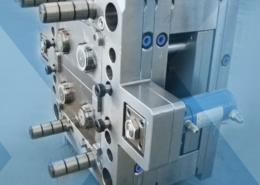
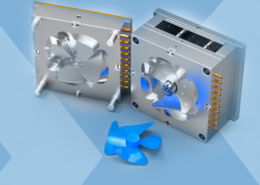
Plastic Molding
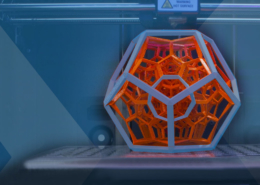
Rapid Prototyping
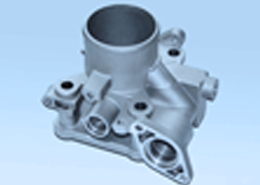
Pressure Die Casting
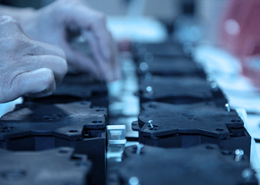
Parts Assembly
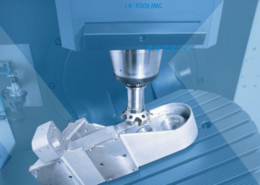