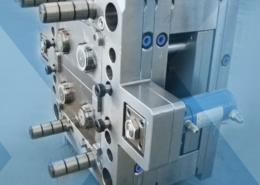
PT Injection Molding: Pioneering Precision Manufacturing
Author:gly Date: 2024-06-08
Introduction: Unveiling the Potential of PT Injection Molding
PT injection molding emerges as a beacon of innovation, captivating the attention of engineers, designers, and manufacturers worldwide. This advanced manufacturing process marries precision and technology, revolutionizing the production of intricate components with unparalleled accuracy and efficiency. As we delve into the intricacies of PT injection molding, we uncover its transformative potential, its diverse applications, and the challenges and opportunities it presents.
The Essence of PT Injection Molding
PT injection molding epitomizes the pinnacle of precision manufacturing, where meticulous attention to detail and cutting-edge technology converge to fabricate components of exceptional quality and complexity. Unlike traditional injection molding techniques, PT injection molding harnesses advanced materials, sophisticated machinery, and precise control systems to achieve micron-level accuracy and consistency. From automotive and aerospace to electronics and medical devices, PT injection molding offers a versatile solution for industries seeking to optimize performance, reduce costs, and accelerate time-to-market.
Advancements in Material Science
One of the key drivers behind the success of PT injection molding is the continuous evolution of materials tailored to meet the demands of modern manufacturing. Advanced polymers, composites, and alloys with enhanced properties such as strength, durability, and thermal stability enable manufacturers to push the boundaries of design and performance. Moreover, innovations in material compounding, blending, and additive manufacturing techniques offer unprecedented versatility, allowing for the creation of tailored formulations to suit specific application requirements.
Optimization of Process Parameters
Central to the success of PT injection molding is the precise control and optimization of process parameters such as temperature, pressure, injection speed, and cooling time. Through the integration of sophisticated automation, sensor technology, and real-time monitoring systems, manufacturers can fine-tune every aspect of the injection molding process, minimizing defects, reducing cycle times, and maximizing productivity. Furthermore, advancements in simulation software enable engineers to conduct virtual experiments, optimizing designs and process parameters before physical production, thus mitigating risks and accelerating innovation.
Challenges and Future Directions
Despite its remarkable capabilities, PT injection molding is not without its challenges. Issues such as part shrinkage, warping, and material degradation pose significant hurdles, necessitating ongoing research and development efforts. Future directions in PT injection molding may involve the integration of artificial intelligence, machine learning, and predictive analytics to further enhance process control, optimize material selection, and anticipate and mitigate potential issues. Moreover, the adoption of sustainable materials and practices is poised to shape the future of PT injection molding, fostering environmental stewardship and reducing the industry's carbon footprint.
Conclusion: Charting a Course for Innovation
In conclusion, PT injection molding stands at the forefront of manufacturing innovation, offering unparalleled precision, efficiency, and versatility across diverse industries. As we look to the future, continued investment in research, collaboration, and technological advancement will drive further progress and unlock new possibilities. By embracing the principles of precision, ingenuity, and sustainability, we can harness the full potential of PT injection molding to propel manufacturing into a new era of excellence and opportunity.
GETTING A QUOTE WITH LK-MOULD IS FREE AND SIMPLE.
FIND MORE OF OUR SERVICES:
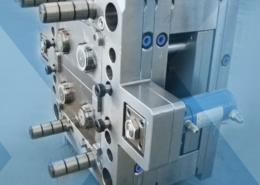
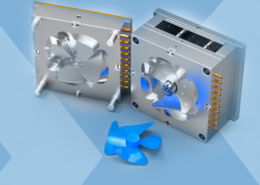
Plastic Molding
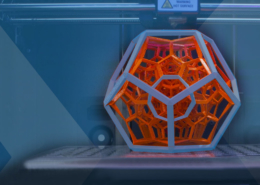
Rapid Prototyping
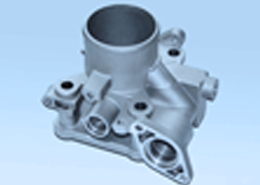
Pressure Die Casting
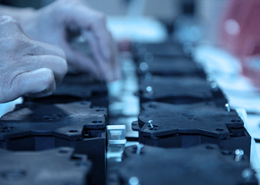
Parts Assembly
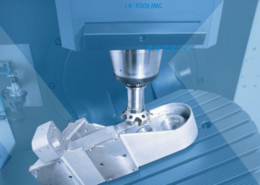