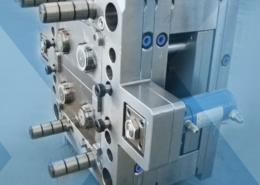
Unraveling the Wonders of Prototype Plastic Molding: A Comprehensive Exploration
Author:gly Date: 2024-06-08
Introduction
Prototype plastic molding stands as a cornerstone of modern manufacturing, offering a gateway to innovation and efficiency. From concept to production, this versatile process holds the key to realizing groundbreaking designs and bringing them to life. In this article, we embark on a journey to unravel the intricacies of prototype plastic molding, delving into its origins, applications, technological advancements, and future prospects.
Background
Prototype plastic molding encompasses a range of techniques aimed at creating preliminary models or samples of plastic components. These prototypes serve as tangible representations of design concepts, allowing engineers and designers to evaluate form, fit, and function before committing to mass production. The evolution of prototype plastic molding can be traced back to the mid-20th century when the advent of plastics revolutionized the manufacturing landscape, offering unprecedented versatility and cost-effectiveness.
Applications
Automotive Industry
In the automotive sector, prototype plastic molding plays a crucial role in the development of vehicle components, ranging from interior trims to structural elements. By enabling rapid iteration and testing of design concepts, manufacturers can accelerate the product development cycle, reduce time-to-market, and enhance overall performance and safety.
Consumer Electronics
The consumer electronics industry relies heavily on prototype plastic molding to iterate and refine designs for smartphones, tablets, wearables, and other gadgets. By leveraging advanced materials and manufacturing techniques, companies can achieve sleek, ergonomic designs that meet the demands of today's tech-savvy consumers.
Medical Devices
Prototype plastic molding holds immense promise in the healthcare domain, facilitating the development of medical devices and equipment. From surgical instruments to diagnostic devices, prototypes enable manufacturers to validate designs, ensure regulatory compliance, and improve patient outcomes through innovation and precision engineering.
Technological Advances
Additive Manufacturing Integration
The integration of additive manufacturing technologies such as 3D printing has revolutionized prototype plastic molding, offering unprecedented design freedom and customization. By layering materials in a precise manner, engineers can create complex geometries and intricate features that were previously unattainable with traditional molding techniques.
Digital Twin Simulation
Digital twin simulation software has emerged as a powerful tool for optimizing the prototype plastic molding process. By creating virtual replicas of molds and simulating the injection molding process, manufacturers can identify potential issues, optimize parameters, and reduce time and costs associated with physical prototyping.
Material Innovations
Advancements in polymer science have led to the development of a wide range of materials tailored for prototype plastic molding. From biodegradable polymers to high-performance engineering resins, these materials offer diverse properties such as strength, flexibility, and heat resistance, catering to the unique requirements of various industries and applications.
Challenges and Considerations
Design Complexity
Complex geometries and intricate features pose challenges in prototype plastic molding, necessitating careful design considerations to ensure manufacturability and part quality. Collaboration between designers, engineers, and molders is essential to optimize designs for the molding process and minimize the risk of defects.
Cost Constraints
Cost considerations remain a critical factor in prototype plastic molding, particularly for small-scale productions and startups. Balancing the trade-offs between prototyping expenses and potential savings in downstream manufacturing is essential for maximizing return on investment and maintaining competitiveness in the market.
Regulatory Compliance
Ensuring regulatory compliance is paramount in industries such as healthcare and automotive, where safety and quality standards are rigorously enforced. Prototypes must undergo thorough testing and validation to ensure compliance with industry regulations and standards, mitigating the risk of liability and product recalls.
Conclusion
In conclusion, prototype plastic molding stands as a testament to human ingenuity and innovation, enabling the creation of groundbreaking products that shape our world. By leveraging technological advancements, addressing key challenges, and embracing a collaborative mindset, manufacturers can unlock new frontiers of possibility and drive sustainable growth in the ever-evolving landscape of manufacturing.
As we look to the future, the continued advancement of prototype plastic molding holds immense promise in accelerating innovation, enhancing competitiveness, and addressing global challenges. By investing in research, education, and cross-disciplinary collaboration, we can harness the full potential of this transformative technology and usher in a new era of manufacturing excellence.
GETTING A QUOTE WITH LK-MOULD IS FREE AND SIMPLE.
FIND MORE OF OUR SERVICES:
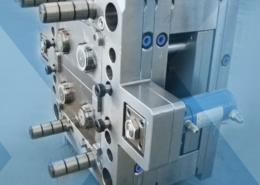
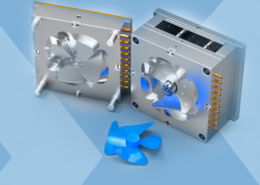
Plastic Molding
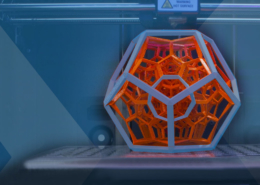
Rapid Prototyping
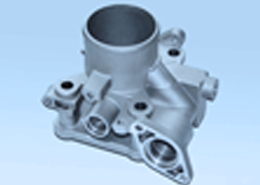
Pressure Die Casting
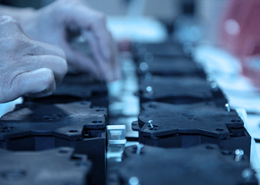
Parts Assembly
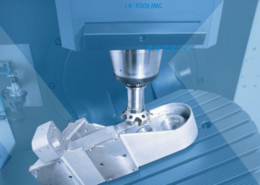