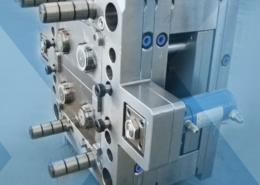
Exploring the Dynamics of Rubber Plastic Molding
Author:gly Date: 2024-06-08
Introduction
Rubber plastic molding stands as a pivotal process at the intersection of rubber and plastic manufacturing, offering a versatile means of producing complex components with a combination of flexibility, resilience, and durability. From automotive seals to consumer electronics enclosures, rubber plastic molding shapes the products we rely on in our daily lives. This article embarks on a comprehensive exploration of rubber plastic molding, shedding light on its methodologies, applications, and the driving forces behind its evolution.
The Fusion of Rubber and Plastic
Rubber plastic molding represents the convergence of two distinct materials, each with its unique properties and applications. By combining the flexibility and elasticity of rubber with the versatility and moldability of plastics, manufacturers can produce components that exhibit a wide range of mechanical and thermal properties. This fusion of materials enables the creation of products that are both resilient and lightweight, catering to diverse industries such as automotive, aerospace, and consumer goods.
Injection Molding Techniques
Injection molding stands as the predominant technique in rubber plastic molding, offering unparalleled precision and efficiency in component production. The process involves injecting molten rubber plastic material into a mold cavity under high pressure, where it solidifies and takes the shape of the mold. Advanced injection molding technologies, such as multi-cavity molds and overmolding, enable the production of complex geometries and assemblies with minimal waste and cycle times.
Materials Selection and Properties
The selection of materials in rubber plastic molding is a critical determinant of part performance, functionality, and durability. Manufacturers must consider factors such as material compatibility, chemical resistance, and mechanical properties when choosing the appropriate rubber plastic blend for a given application. Silicone rubber, for instance, offers superior heat resistance and biocompatibility, making it ideal for medical and food-grade applications, while thermoplastic elastomers (TPEs) combine the properties of rubber and plastic for applications requiring flexibility and impact resistance.
Applications Across Industries
Rubber plastic molding finds widespread application across a myriad of industries, from automotive and aerospace to healthcare and consumer electronics. In the automotive sector, it is used to produce seals, gaskets, and interior trim components, contributing to vehicle comfort, safety, and performance. In the medical field, rubber plastic molding is employed to fabricate medical device components and implants, where biocompatibility and precision are paramount. Moreover, consumer electronics benefit from the aesthetic appeal and durability of rubber plastic components, enhancing product reliability and user experience.
Quality Assurance and Process Optimization
Ensuring the quality and consistency of rubber plastic molded parts is essential to their performance and reliability. Manufacturers employ rigorous quality assurance protocols, including dimensional inspection, material testing, and visual inspection, to detect defects and deviations from specifications. Additionally, process optimization techniques, such as Design of Experiments (DOE) and Six Sigma methodologies, enable manufacturers to fine-tune production processes, minimize variability, and maximize yield rates, ultimately delivering superior quality components to end-users.
Conclusion
In conclusion, rubber plastic molding stands as a testament to the ingenuity and versatility of modern manufacturing techniques. By harnessing the synergies between rubber and plastic materials, manufacturers can produce components that embody the best of both worlds – flexibility, resilience, and precision. As we navigate towards a future characterized by innovation and sustainability, continued research and collaboration will drive the evolution of rubber plastic molding, reshaping industries and enriching lives.
GETTING A QUOTE WITH LK-MOULD IS FREE AND SIMPLE.
FIND MORE OF OUR SERVICES:
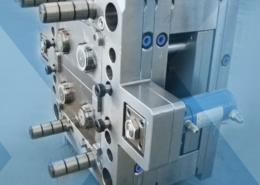
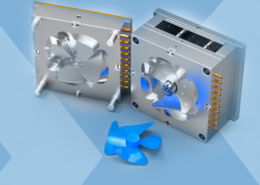
Plastic Molding
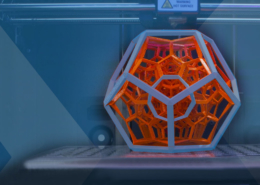
Rapid Prototyping
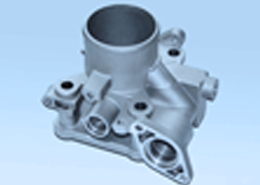
Pressure Die Casting
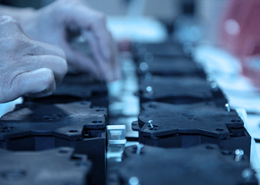
Parts Assembly
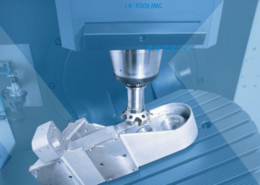