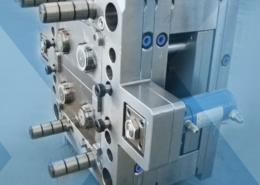
Exploring Scientific Injection Molding: Revolutionizing Plastic Manufacturing
Author:gly Date: 2024-06-08
Scientific Injection Molding (SIM) stands as a pinnacle in the realm of plastic manufacturing, heralding a new era of precision, efficiency, and quality. This advanced methodology integrates scientific principles with the art of molding, elevating the process from a mere production technique to a sophisticated science.
The Essence of Scientific Injection Molding
Scientific Injection Molding epitomizes a fusion of meticulous engineering and empirical science. It harnesses the power of data-driven insights, computational modeling, and empirical analysis to optimize every facet of the injection molding process. From material selection to tool design, and from process optimization to quality assurance, SIM meticulously scrutinizes each element to achieve unparalleled precision and consistency.
Key Components and Parameters
At the core of Scientific Injection Molding lies a comprehensive understanding of the key components and parameters influencing the process. Temperature, pressure, flow rate, cooling time, and material properties emerge as critical variables meticulously controlled and optimized through empirical experimentation and computational simulations. By meticulously fine-tuning these parameters, manufacturers can achieve optimal part quality, dimensional accuracy, and production efficiency.
Advantages and Applications
The adoption of Scientific Injection Molding bestows a plethora of advantages across various industries. From automotive and aerospace to medical and consumer goods, the precision and repeatability offered by SIM revolutionize product design and manufacturing. Enhanced part quality, reduced cycle times, minimized material wastage, and improved production scalability stand as testament to the transformative impact of this methodology.
Challenges and Future Directions
Despite its remarkable advancements, Scientific Injection Molding is not without its challenges. The complexities of process optimization, material characterization, and tooling design pose ongoing hurdles for manufacturers. Moreover, the advent of novel materials, additive manufacturing technologies, and Industry 4.0 principles necessitate continuous evolution and innovation within the realm of SIM. Future research endeavors must focus on integrating advanced analytics, machine learning algorithms, and real-time monitoring systems to further enhance the precision, efficiency, and sustainability of injection molding processes.
Conclusion
In conclusion, Scientific Injection Molding represents a paradigm shift in plastic manufacturing, transcending traditional boundaries and unlocking new frontiers of possibility. Through a synergistic blend of scientific rigor, engineering expertise, and technological innovation, SIM empowers manufacturers to realize unprecedented levels of precision, efficiency, and quality in their products. As we venture into the future, embracing the principles of Scientific Injection Molding will be instrumental in driving sustainable growth, innovation, and competitiveness across industries worldwide.
GETTING A QUOTE WITH LK-MOULD IS FREE AND SIMPLE.
FIND MORE OF OUR SERVICES:
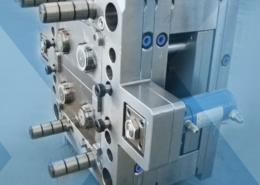
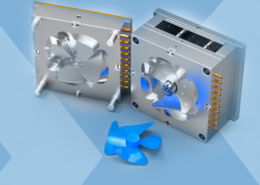
Plastic Molding
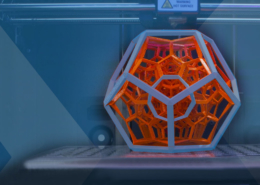
Rapid Prototyping
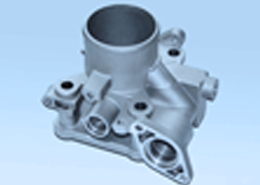
Pressure Die Casting
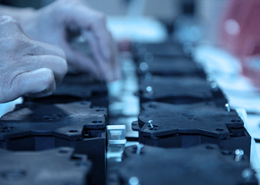
Parts Assembly
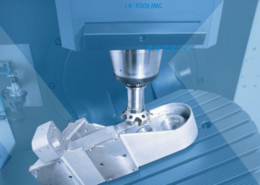