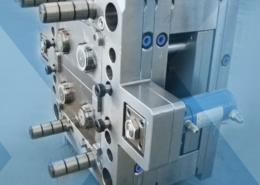
Exploring the Dynamics of Slide Injection Molding
Author:gly Date: 2024-06-08
Introduction:
Slide injection molding stands as a sophisticated variant of conventional injection molding, offering enhanced capabilities in producing intricate and multi-component plastic parts. This process involves the use of sliding mechanisms within the mold to facilitate the injection of plastic materials into complex geometries. In this article, we delve into the nuances of slide injection molding, examining its principles, applications, advantages, and future prospects.
Understanding Slide Injection Molding
Slide injection molding, also known as side action molding or core-pulling molding, employs sliding mechanisms within the mold to create undercuts, threads, holes, or other complex features in the molded part. Unlike standard injection molding, which relies solely on the opening and closing of the mold halves, slide injection molding introduces additional movement perpendicular to the direction of mold opening. This enables the production of parts with intricate details and non-linear geometries, expanding the design possibilities for manufacturers.
The sliding mechanisms, often driven by hydraulic, pneumatic, or mechanical actuators, are integrated into the mold design to facilitate precise and synchronized movement during the injection process. These slides, cores, or lifters operate in coordination with the injection molding machine, ensuring optimal filling of the mold cavity and ejection of the finished part. The intricate interplay between mold design, material selection, and process parameters is crucial in achieving consistent and high-quality results in slide injection molding.
Applications and Industries
Slide injection molding finds widespread use across various industries, particularly in the production of components with complex geometries and tight tolerances. In the automotive sector, it is employed in the fabrication of interior trim panels, dashboard components, and intricate connectors. The consumer electronics industry utilizes slide injection molding for producing casings, housings, and button assemblies with ergonomic designs and integrated features. Moreover, medical device manufacturers leverage this process for creating surgical instruments, implants, and drug delivery devices with intricate geometries and precise functionalities.
Beyond these traditional applications, slide injection molding offers novel possibilities in fields such as aerospace, telecommunications, and consumer goods. Its ability to integrate multiple materials, colors, and textures within a single part enables innovative designs and enhanced product functionality. Furthermore, the scalability and repeatability of slide injection molding make it suitable for both prototyping and high-volume production, catering to diverse manufacturing needs across industries.
Advantages and Challenges
The adoption of slide injection molding offers several advantages over conventional molding processes. Firstly, it allows for the production of complex parts with undercuts, threads, or internal features that would be impossible or costly to achieve using standard methods. Secondly, it enables the integration of multiple components into a single molded part, reducing assembly time, costs, and potential points of failure. Additionally, slide injection molding enhances design flexibility, enabling engineers to realize intricate geometries and innovative product features.
However, slide injection molding also presents certain challenges, particularly in terms of mold complexity, cycle time, and tooling costs. The design and fabrication of molds with sliding mechanisms require specialized expertise and precision machining, increasing upfront investment and lead times. Moreover, the additional movement involved in slide injection molding can extend cycle times and affect production efficiency, especially for large or intricate parts. Addressing these challenges necessitates a thorough understanding of mold design principles, material behavior, and process optimization techniques.
Future Directions and Innovations
Looking ahead, the future of slide injection molding holds promise for further innovation and advancement. The integration of advanced materials, such as biodegradable polymers, fiber-reinforced composites, and conductive additives, expands the functional capabilities and sustainability of slide-molded parts. Moreover, the adoption of digital technologies, such as computer-aided design (CAD), simulation software, and additive manufacturing, enables virtual prototyping, design optimization, and rapid tooling fabrication.
Furthermore, the convergence of slide injection molding with Industry 4.0 principles, such as automation, connectivity, and data analytics, paves the way for smart factories and predictive maintenance strategies. Real-time monitoring of process parameters, mold conditions, and part quality facilitates proactive decision-making and continuous improvement, optimizing production efficiency and minimizing downtime. By embracing these innovations and trends, the realm of slide injection molding remains poised for a future defined by precision, versatility, and sustainability.
In conclusion, slide injection molding represents a pinnacle of engineering ingenuity and manufacturing excellence, enabling the production of intricate and multi-component plastic parts with unparalleled precision and efficiency. Its application spans a multitude of industries, from automotive to medical devices, driving innovation and pushing the boundaries of design and functionality. As we embrace new materials, technologies, and methodologies, slide injection molding continues to shape the landscape of modern manufacturing, offering endless possibilities for creativity, customization, and efficiency.
GETTING A QUOTE WITH LK-MOULD IS FREE AND SIMPLE.
FIND MORE OF OUR SERVICES:
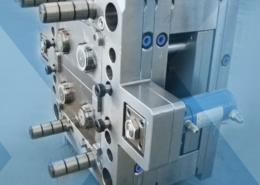
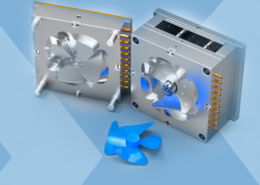
Plastic Molding
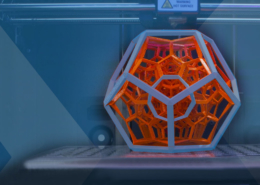
Rapid Prototyping
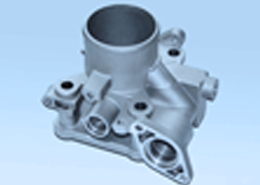
Pressure Die Casting
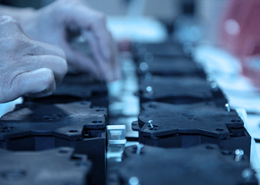
Parts Assembly
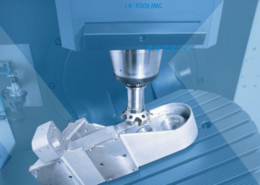