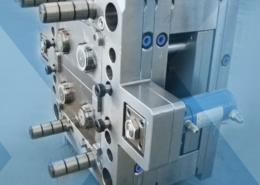
Unveiling the Potential of Short Molds in Injection Molding
Author:gly Date: 2024-06-08
The realm of injection molding continues to witness innovations aimed at enhancing efficiency, reducing costs, and improving product quality. Among these innovations, short molds have emerged as a promising solution with the potential to revolutionize the injection molding process. In this exploration, we delve into the intricacies of short molds in injection molding, uncovering their benefits, applications, and future prospects.
Understanding Short Molds: A Brief Introduction
Short molds, also known as compact molds or mini molds, represent a departure from traditional injection molding techniques by incorporating a shorter mold cavity height. Unlike conventional molds, which feature standard cavity depths, short molds offer a more compact design, resulting in reduced material consumption, shorter cycle times, and enhanced production efficiency.
Background and Evolution
The concept of short molds traces its origins to the need for optimizing the injection molding process in industries characterized by high-volume production and tight space constraints. Over the years, advancements in mold design, materials, and manufacturing technologies have facilitated the development and adoption of short molds across diverse applications, ranging from automotive and electronics to medical devices and consumer goods.
Key Characteristics
Short molds are characterized by their reduced cavity height, which allows for a more streamlined and efficient injection molding process. By minimizing the distance between the mold halves, short molds enable faster cooling times, reduced energy consumption, and increased productivity. Additionally, the compact design of short molds offers greater flexibility in machine selection and layout, making them ideal for space-constrained manufacturing environments.
Advantages and Benefits of Short Molds
The adoption of short molds in injection molding offers a multitude of advantages and benefits, contributing to improved performance, cost savings, and sustainability.
Enhanced Efficiency
Short molds facilitate shorter cycle times and faster production rates, resulting in increased throughput and reduced lead times. By minimizing the distance traveled by the molten material, short molds optimize the injection molding process, leading to higher efficiency and productivity.
Cost Reduction
The compact design of short molds translates into reduced material consumption and lower production costs. Additionally, the faster cycle times enabled by short molds result in decreased energy consumption and operational expenses, further contributing to cost savings for manufacturers.
Improved Quality
Short molds offer enhanced control over the injection molding process, resulting in improved part quality and consistency. The shorter cavity height reduces the risk of material degradation and warping, ensuring the integrity of the final products. Moreover, the optimized cooling characteristics of short molds contribute to reduced cycle variability and fewer defects.
Applications and Case Studies
Short molds find application across a wide range of industries and product categories, demonstrating their versatility and effectiveness in diverse manufacturing environments.
Automotive Industry
In the automotive sector, short molds are utilized for producing lightweight components, such as interior trim panels, dashboard components, and exterior body parts. The compact design of short molds enables efficient production processes while meeting stringent quality and performance requirements.
Electronics and Consumer Goods
In the realm of electronics and consumer goods, short molds are employed for manufacturing miniature components, housings, and enclosures. The reduced cavity height of short molds allows for precise molding of intricate geometries, ensuring optimal functionality and aesthetics for electronic devices and consumer products.
Medical Devices and Healthcare
Short molds play a critical role in the production of medical devices and healthcare products, including syringes, surgical instruments, and diagnostic equipment. The compact design and enhanced efficiency of short molds enable manufacturers to meet the stringent regulatory standards and quality requirements of the medical industry.
Future Directions and Potential Areas of Research
Looking ahead, the continued advancement of short molds in injection molding holds immense potential for further innovation and optimization. Future research efforts may focus on:
Material Compatibility
: Exploring new materials and formulations optimized for use in short molds to enhance performance and durability.
Process Optimization
: Investigating novel process parameters and methodologies to maximize the efficiency and effectiveness of short mold injection molding.
Sustainability
: Addressing environmental concerns and promoting sustainable practices in short mold manufacturing through recycling, waste reduction, and energy efficiency initiatives.
Conclusion: Embracing Innovation in Injection Molding
In conclusion, short molds represent a transformative innovation in the field of injection molding, offering numerous advantages in terms of efficiency, cost savings, and quality improvement. By embracing the potential of short molds and leveraging advanced technologies, manufacturers can unlock new opportunities for enhancing competitiveness and driving sustainable growth. As we continue to explore the capabilities of short molds and push the boundaries of injection molding technology, the future holds exciting possibilities for innovation and advancement in manufacturing.
GETTING A QUOTE WITH LK-MOULD IS FREE AND SIMPLE.
FIND MORE OF OUR SERVICES:
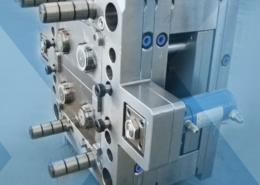
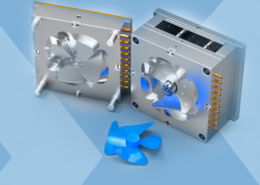
Plastic Molding
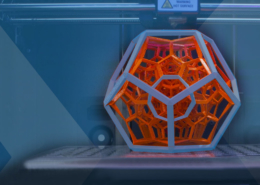
Rapid Prototyping
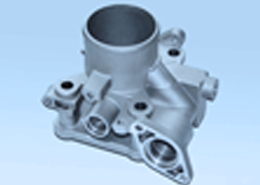
Pressure Die Casting
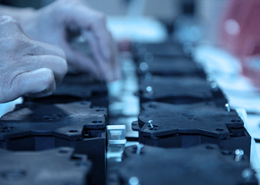
Parts Assembly
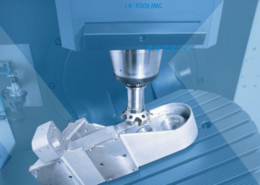