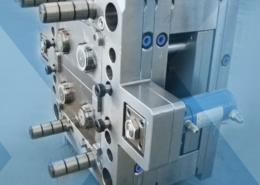
Exploring Thermolator Injection Molding: Revolutionizing Manufacturing Processes
Author:gly Date: 2024-06-08
Introduction
The integration of advanced technologies in manufacturing processes has led to significant advancements in efficiency and quality. One such innovation is Thermolator injection molding, a technique that has revolutionized the production of plastic components. This article aims to delve into the intricacies of Thermolator injection molding, providing readers with a comprehensive understanding of its mechanisms, applications, advantages, and future prospects.
Mechanism of Thermolator Injection Molding
The Process
Thermolator injection molding involves the precise heating of thermoplastic materials to their melting point, followed by the injection of the molten material into a mold cavity. This process is facilitated by a Thermolator unit, which regulates temperature and pressure to ensure optimal molding conditions.
Temperature Control
One of the key features of Thermolator injection molding is its ability to maintain consistent temperatures throughout the molding process. This is achieved through advanced temperature control systems, which monitor and adjust the temperature of the molten material and mold cavity in real-time.
Injection Molding Machine
The injection molding machine plays a crucial role in Thermolator injection molding, as it is responsible for heating, injecting, and cooling the thermoplastic material. These machines are equipped with sophisticated control systems and high-pressure injection mechanisms to ensure precision and accuracy.
Applications of Thermolator Injection Molding
Automotive Industry
Thermolator injection molding finds extensive use in the automotive industry for the production of various components such as interior trim, exterior body panels, and engine parts. The ability to produce complex shapes with high precision makes it an ideal choice for automotive manufacturers.
Consumer Electronics
In the consumer electronics sector, Thermolator injection molding is utilized for the fabrication of casings, connectors, and other intricate components. Its versatility and cost-effectiveness make it a preferred method for mass production of electronic devices.
Medical Devices
The medical industry relies on Thermolator injection molding for the manufacturing of disposable syringes, surgical instruments, and medical implants. The biocompatibility of thermoplastic materials ensures that the final products meet stringent safety and regulatory standards.
Advantages of Thermolator Injection Molding
Cost Efficiency
Compared to traditional manufacturing methods, Thermolator injection molding offers significant cost savings due to reduced material waste, shorter production cycles, and lower labor costs. This makes it an attractive option for businesses aiming to streamline their production processes.
High Precision
Thermolator injection molding enables the production of highly precise and intricate components with minimal variation. The ability to control temperature, pressure, and flow rate ensures consistent quality and dimensional accuracy, meeting the strictest tolerances.
Versatility
One of the most notable advantages of Thermolator injection molding is its versatility in accommodating a wide range of thermoplastic materials. This flexibility allows manufacturers to choose materials with specific properties such as strength, flexibility, and chemical resistance to suit diverse application requirements.
Future Prospects and Recommendations
As technology continues to advance, Thermolator injection molding is poised to further revolutionize the manufacturing industry. Future research and development efforts should focus on enhancing process automation, improving material compatibility, and reducing environmental impact through sustainable practices. By harnessing the full potential of Thermolator injection molding, manufacturers can unlock new opportunities for innovation and growth.
Conclusion
In conclusion, Thermolator injection molding stands as a cornerstone of modern manufacturing, offering unparalleled precision, efficiency, and versatility. By understanding its mechanisms, applications, advantages, and future prospects, businesses can harness the power of this technology to drive progress and innovation in their respective industries. As we look towards the future, continued advancements in Thermolator injection molding are poised to reshape the landscape of manufacturing, paving the way for a more sustainable and prosperous future.
GETTING A QUOTE WITH LK-MOULD IS FREE AND SIMPLE.
FIND MORE OF OUR SERVICES:
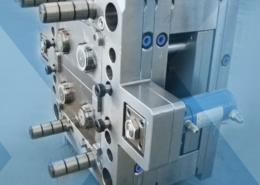
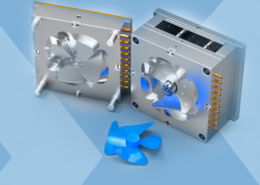
Plastic Molding
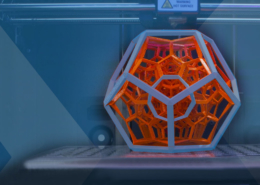
Rapid Prototyping
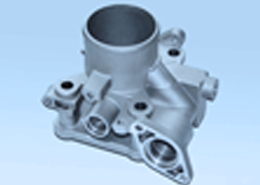
Pressure Die Casting
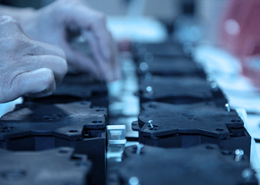
Parts Assembly
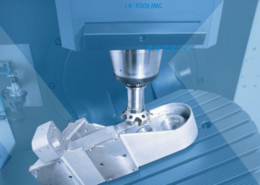