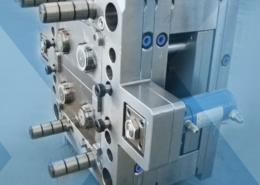
Unraveling the World of Thermoplastic Molding
Author:gly Date: 2024-06-08
Thermoplastic molding stands as a cornerstone in the realm of manufacturing, offering a versatile and efficient method for producing a myriad of plastic components. From automotive parts to consumer electronics, the process of thermoplastic molding plays a crucial role in shaping various industries. This article aims to explore the intricacies of thermoplastic molding, providing readers with insights into its processes, applications, and significance in the modern manufacturing landscape.
Introduction to Thermoplastic Molding
Thermoplastic molding refers to a manufacturing process wherein thermoplastic polymers are melted, shaped, and solidified to form intricate components. Unlike thermoset materials, which undergo irreversible chemical changes during the molding process, thermoplastics can be repeatedly melted and reformed, making them highly versatile and cost-effective. This characteristic has propelled thermoplastic molding into one of the most widely used manufacturing techniques across diverse industries.
Process Overview and Variants
The process of thermoplastic molding encompasses various techniques, each tailored to meet specific requirements in terms of complexity, volume, and precision. Injection molding, the most common method, involves injecting molten thermoplastic material into a mold cavity under high pressure. This results in the formation of the desired shape upon cooling. Other variants include blow molding, extrusion molding, and compression molding, each offering unique advantages in terms of scalability, design flexibility, and production speed.
Advantages and Challenges
Thermoplastic molding offers a plethora of advantages, making it a preferred choice for manufacturers worldwide. Its ability to produce complex geometries with high precision ensures consistent quality and dimensional accuracy, essential for industries such as aerospace and medical devices. Moreover, the relatively low tooling costs and short lead times associated with thermoplastic molding make it an economically viable option for both prototyping and mass production.
However, the process is not without its challenges. Factors such as material selection, mold design, and process optimization significantly impact the quality and efficiency of thermoplastic molding operations. Moreover, ensuring uniform cooling and minimizing warpage are critical considerations, particularly for large and intricate parts. Addressing these challenges requires a comprehensive understanding of material properties, process parameters, and tooling design, highlighting the importance of expertise and experience in thermoplastic molding.
Applications and Future Trends
The applications of thermoplastic molding span across a wide range of industries, from automotive and aerospace to healthcare and consumer goods. Its versatility and scalability make it suitable for producing components of varying sizes and complexities, ranging from microfluidic devices to structural components in automobiles.
Looking ahead, the future of thermoplastic molding lies in embracing advancements in materials science, automation, and digitalization. The development of high-performance thermoplastics with enhanced mechanical properties and sustainability profiles opens up new avenues for innovation and product differentiation. Furthermore, the integration of artificial intelligence and machine learning technologies can optimize process parameters and predictive maintenance, further enhancing efficiency and productivity.
In conclusion, thermoplastic molding stands as a cornerstone in modern manufacturing, offering unparalleled versatility, efficiency, and scalability. By understanding its processes, advantages, and challenges, manufacturers can harness the full potential of thermoplastic molding to drive innovation and meet the demands of an ever-evolving market landscape.
GETTING A QUOTE WITH LK-MOULD IS FREE AND SIMPLE.
FIND MORE OF OUR SERVICES:
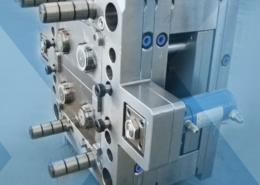
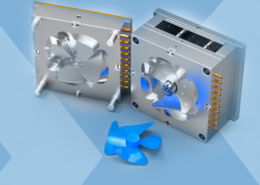
Plastic Molding
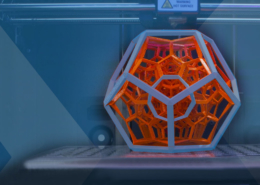
Rapid Prototyping
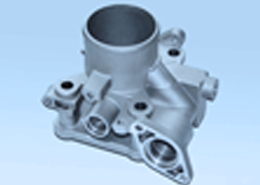
Pressure Die Casting
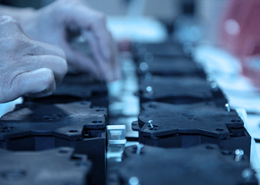
Parts Assembly
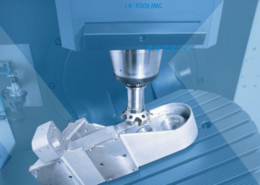