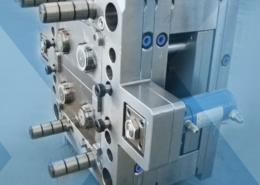
Demystifying Injection Molding for Beginners
Author:gly Date: 2024-06-08
Introduction: Piquing Curiosity
"Injection Molding for Dummies" serves as a gateway for novices to delve into the fascinating world of plastic manufacturing. For those unfamiliar with the process, injection molding might seem like a complex endeavor shrouded in technical jargon. However, as we peel back the layers, we discover a straightforward and immensely versatile technique that underpins the production of countless everyday items. In this article, we embark on a journey to demystify injection molding, offering insights into its fundamentals, applications, and potential for innovation.
1. Understanding the Basics
At its core, injection molding involves the injection of molten plastic material into a mold cavity, where it solidifies to form a desired shape. The process consists of several key stages, including material preparation, injection, cooling, and ejection. Each step is meticulously controlled to ensure the production of high-quality parts with minimal defects.
To illustrate, consider the example of manufacturing a plastic bottle using injection molding. The process begins with the melting of plastic pellets in a heated barrel, followed by the injection of the molten material into a bottle-shaped mold. After cooling and solidification, the mold opens, and the finished bottle is ejected, ready for further processing or packaging.
2. Applications Across Industries
Injection molding finds widespread applications across various industries, ranging from automotive and electronics to medical devices and consumer goods. In the automotive sector, it is used for producing interior components, exterior trims, and structural parts, where lightweight and durable materials are essential.
Similarly, in the electronics industry, injection molding enables the fabrication of housings, enclosures, and connectors for electronic devices, ensuring precise fit and protection against environmental factors. Moreover, in the medical field, injection molding is utilized for manufacturing surgical instruments, medical implants, and disposable devices, where biocompatibility and sterilizability are critical.
3. Key Considerations for Success
While injection molding offers numerous advantages in terms of efficiency and versatility, achieving optimal results requires careful consideration of various factors. These include mold design, material selection, process parameters, and quality control measures.
For instance, the design of the mold plays a crucial role in determining part quality and manufacturability. Complex geometries, undercuts, and thin-wall sections may pose challenges that need to be addressed through innovative mold design solutions. Additionally, selecting the appropriate plastic resin based on mechanical properties, chemical resistance, and cost considerations is essential for meeting performance requirements and regulatory standards.
4. Future Directions and Innovations
Looking ahead, the future of injection molding holds exciting prospects for innovation and advancement. Emerging trends such as additive manufacturing, multi-material molding, and Industry 4.0 integration are poised to reshape the landscape of plastic manufacturing.
Additive manufacturing techniques like 3D printing offer new possibilities for rapid prototyping, customized production, and on-demand manufacturing. Multi-material molding enables the integration of different plastics or even metals within a single part, unlocking new design possibilities and functional capabilities. Furthermore, the integration of data analytics, IoT connectivity, and AI-driven optimization algorithms holds the potential to enhance process efficiency, quality control, and predictive maintenance.
Conclusion: Empowering Novices, Inspiring Innovation
In conclusion, "Injection Molding for Dummies" serves as a gateway for beginners to explore the intricacies of plastic manufacturing and discover its vast potential. By understanding the fundamentals, exploring real-world applications, and embracing innovation, novices can embark on a journey of learning and discovery in the realm of injection molding.
As we navigate the complexities of the modern industrial landscape, let us embrace the principles of continuous improvement, collaboration, and innovation. By empowering novices with knowledge and fostering a culture of creativity and exploration, we can unlock new frontiers in injection molding and drive meaningful advancements in technology, sustainability, and societal well-being.
GETTING A QUOTE WITH LK-MOULD IS FREE AND SIMPLE.
FIND MORE OF OUR SERVICES:
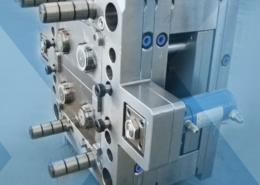
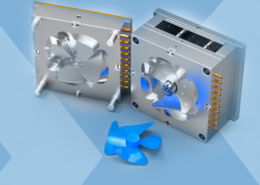
Plastic Molding
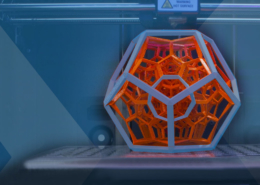
Rapid Prototyping
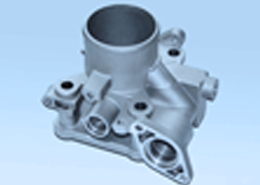
Pressure Die Casting
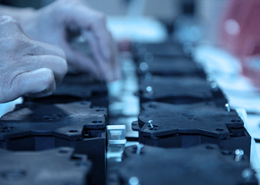
Parts Assembly
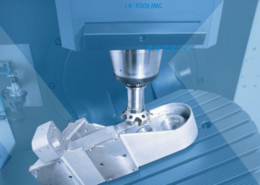