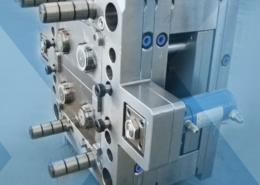
Exploring the Marvels of Injection Molding LEGO
Author:gly Date: 2024-06-08
Lego, a beloved toy cherished by generations, owes its intricate designs and seamless assembly to the marvels of injection molding. This manufacturing technique has revolutionized the toy industry, enabling the production of intricate and durable plastic pieces on a massive scale. In this article, we delve into the world of injection molding Lego, uncovering its secrets and exploring its significance.
The Art of Injection Molding
Injection molding stands as a pinnacle of modern manufacturing, allowing for the mass production of intricate plastic components with unparalleled precision. At its core, the process involves injecting molten plastic material into a mold cavity, where it solidifies to form the desired shape. Lego, with its precise dimensions and intricate details, exemplifies the perfection achievable through injection molding.
The process begins with the design of the mold, meticulously crafted to capture every detail of the desired Lego piece. Advanced CAD software enables engineers to create molds with micron-level precision, ensuring that each piece fits seamlessly with its counterparts. Once the mold is ready, it undergoes rigorous testing to ensure quality and durability.
Material Matters: The Science Behind Lego Plastic
The choice of plastic material is crucial in injection molding, influencing the durability, flexibility, and aesthetics of the final product. Lego utilizes acrylonitrile butadiene styrene (ABS) plastic, prized for its strength, impact resistance, and ability to retain vibrant colors. This high-quality material ensures that Lego pieces withstand the test of time, enduring countless hours of play without losing their shape or color.
Precision Engineering: Ensuring Perfect Fit
One of the hallmarks of Lego is its precision engineering, which allows pieces manufactured decades apart to seamlessly interlock. This feat is achieved through meticulous attention to detail during the injection molding process. Each mold cavity is engineered with precision to ensure that every Lego piece meets the exacting standards set by the company. As a result, builders can create intricate structures with confidence, knowing that each piece will fit perfectly into place.
Sustainability: Towards a Greener Future
While injection molding has revolutionized the toy industry, it also poses environmental challenges due to its reliance on plastic materials. However, Lego has taken significant strides towards sustainability, committing to using plant-based plastics and investing in recycling initiatives. By embracing eco-friendly practices, Lego aims to reduce its environmental footprint while continuing to inspire creativity and innovation.
Conclusion: Shaping the Future of Play
In conclusion, injection molding has played a pivotal role in shaping the iconic Lego bricks that have captivated the imaginations of millions worldwide. From precision engineering to sustainable practices, every aspect of the manufacturing process reflects Lego's commitment to quality and innovation. As we look towards the future, the legacy of injection molding Lego serves as a testament to the power of creativity and engineering ingenuity. By continuing to push the boundaries of manufacturing technology and embracing sustainable practices, Lego is poised to inspire future generations for years to come.
GETTING A QUOTE WITH LK-MOULD IS FREE AND SIMPLE.
FIND MORE OF OUR SERVICES:
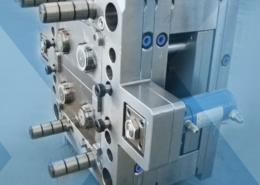
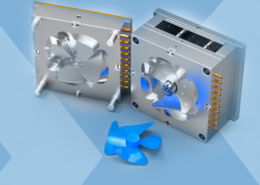
Plastic Molding
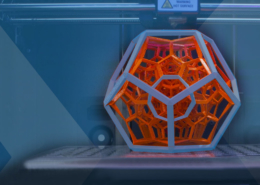
Rapid Prototyping
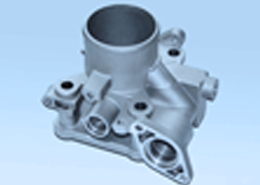
Pressure Die Casting
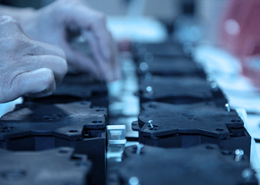
Parts Assembly
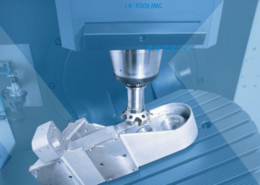