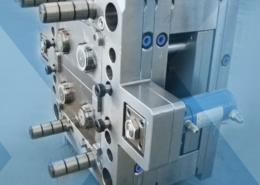
Exploring the Versatility of L-Shaped Plastic Molding: Design, Functionality, an
Author:gly Date: 2024-06-08
Introduction
L-shaped plastic molding represents a fundamental technique in modern manufacturing, offering a versatile solution for producing components with complex geometries and enhanced functionality. This article embarks on a journey to unravel the intricacies of L-shaped plastic molding, shedding light on its applications, advantages, and transformative potential in various industries.
Unveiling the Essence of L-Shaped Plastic Molding
L-shaped plastic molding involves the fabrication of plastic components with an L-shaped profile, characterized by perpendicular or angled edges. This technique enables the production of parts with unique geometries and enhanced functionality, making it indispensable in applications ranging from furniture and construction to automotive and electronics.
Enhancing Structural Integrity and Stability
One of the key advantages of L-shaped plastic molding lies in its ability to enhance structural integrity and stability in components. The L-shaped profile provides increased rigidity and strength, allowing for the creation of robust parts capable of withstanding mechanical stresses and environmental factors.
Moreover, the perpendicular or angled edges of L-shaped components facilitate easy integration into assemblies and structures, providing additional support and reinforcement where needed. This makes L-shaped plastic molding ideal for applications where structural integrity and stability are paramount, such as architectural elements and load-bearing components.
Optimizing Space Utilization and Functionality
L-shaped plastic molding offers significant advantages in terms of space utilization and functionality, especially in constrained environments or tight spaces. The compact design of L-shaped components allows for efficient use of available space, maximizing storage capacity and minimizing wastage.
Furthermore, the unique geometry of L-shaped components enables the creation of functional features such as mounting points, channels, and interfaces, enhancing their versatility and usability. Whether it's optimizing storage solutions in residential settings or maximizing efficiency in industrial environments, L-shaped plastic molding offers endless possibilities for space optimization and functional integration.
Facilitating Design Flexibility and Customization
L-shaped plastic molding empowers designers and engineers with unparalleled flexibility and customization options. The ability to vary the dimensions, angles, and configurations of L-shaped components allows for tailored solutions that meet specific application requirements and design preferences.
Additionally, L-shaped plastic molding techniques such as injection molding and extrusion offer versatility in material selection, allowing for the use of a wide range of thermoplastics with varying properties and characteristics. This enables designers to optimize material selection based on factors such as strength, durability, and cost, ensuring that L-shaped components meet the performance requirements of diverse applications.
Conclusion
In conclusion, L-shaped plastic molding stands as a testament to the convergence of design, functionality, and versatility in modern manufacturing. From enhancing structural integrity and stability to optimizing space utilization and functionality, L-shaped plastic molding offers unparalleled advantages across a wide range of industries.
Looking ahead, the continued evolution and adoption of L-shaped plastic molding technology hold significant promise for driving innovation and advancement in various fields. By embracing this transformative technique and pushing the boundaries of what's possible, manufacturers can unlock new opportunities for design innovation, product differentiation, and market competitiveness.
GETTING A QUOTE WITH LK-MOULD IS FREE AND SIMPLE.
FIND MORE OF OUR SERVICES:
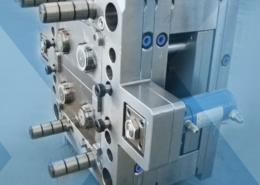
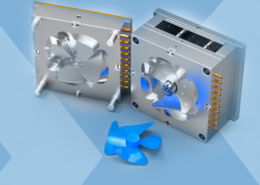
Plastic Molding
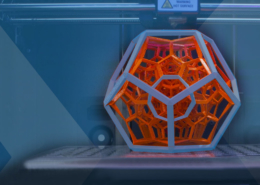
Rapid Prototyping
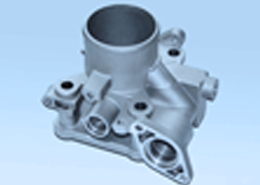
Pressure Die Casting
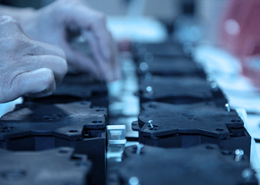
Parts Assembly
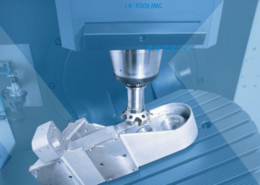