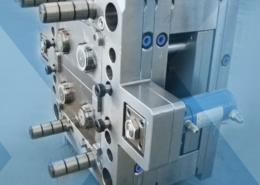
The Essentials of Plastic Mold Design and Manufacturing
Author:gly Date: 2024-06-01
The article delves into the intricacies of plastic mold design and manufacturing, discussing the critical role of molds in the plastic industry, types of plastic molds, design considerations, manufacturing processes, and advancements in mold technology.
Introduction
In the world of plastic manufacturing, molds play a pivotal role in shaping our everyday lives. They are the unsung heroes of the industry, silently transforming liquid plastic into solid, functional products with precision and efficiency. From simple household items to complex industrial components, plastic molds are essential for realizing the diverse range of shapes and sizes required in the market.
Types of Plastic Molds
Plastic molds can be classified into several types depending on their purpose, complexity, and application. Some common types include:
1. Injection Molds: These are the most widely used type of plastic molds, used for mass production of identical parts. Injection molding involves injecting molten plastic into a mold cavity, which solidifies to form the desired shape.
2. Compression Molds : These molds are used for molding thermosetting plastics, which do not melt but rather solidify under pressure. Compression molding involves applying pressure to the material placed within the mold cavity, resulting in its compaction and curing.
3. Transfer Molds: Transfer molding is similar to injection molding but uses a transfer machine to feed the molten plastic into the mold cavity. This process is often used for small, intricate parts.
4. Blow Molds: Blow molding is commonly used for creating hollow plastic parts, such as bottles and containers. A molten plastic tube is extruded into a mold cavity, and air is then blown into the tube, causing it to expand and conform to the shape of the mold.
Design Considerations for Plastic Molds
Designing a plastic mold involves meticulous planning and consideration of various factors. Here are some key considerations:
1. Part Geometry: The geometry of the desired plastic part directly affects the mold design. Complex shapes require more intricate mold cavities, while simpler shapes allow for straightforward mold designs.
2. Material Selection: Choosing the right plastic material is crucial as it determines the part's properties, such as strength, durability, and cost. The selected material must be compatible with the molding process and meet the end-use requirements.
3. Ejection System: The ejection system is responsible for ejecting the molded part from the mold cavity. It must be designed to ensure a smooth and uniform ejection process, avoiding part damage or deformation.
4. Cooling System: Effective cooling is essential for ensuring uniform cooling of the molded part and preventing warping or distortion. The mold design must incorporate an efficient cooling system, such as cooling channels or water lines.
5. Parting Lines: Parting lines are the lines where the mold halves meet and separate during the molding process. They must be carefully designed to ensure a clean, seamless finish on the molded part.
Manufacturing Processes for Plastic Molds:
Manufacturing plastic molds involves several stages, including:
1. Mold Base Construction**: The mold base provides the structural support for the mold and is usually made from steel or aluminum. It is precision-machined to ensure accurate alignment of the mold halves.
2. Cavity and Core Fabrication**: The cavity and core are the two halves of the mold that define the shape of the molded part. They are fabricated using machining processes such as milling, turning, and grinding to achieve the desired shape and finish.
3. Ejection System Installation**: The ejection system, including ejector pins and plates, is installed to facilitate the removal of the molded part from the mold cavity.
4. Cooling System Integration**: Cooling channels or water lines are incorporated into the mold to ensure effective cooling of the molded part during the molding process.
5. Assembly and Testing**: Once all components are fabricated and assembled, the mold is tested to ensure it functions properly and produces defect-free parts. This involves performing trial runs and checking the part's dimensions, tolerances, and surface finish.
Advancements in Mold Technology:
With the constant evolution of technology, mold design and manufacturing have also witnessed significant advancements. Some of the recent trends and developments in mold technology include:
1. CAD/CAM/CAE Software: The integration of advanced CAD/CAM/CAE software has significantly streamlined the mold design and manufacturing process. These software tools allow for faster, more accurate mold design, simulation of the molding process, and optimization of mold performance.
2. Automated Manufacturing: Automation has revolutionized mold manufacturing, increasing productivity and reducing lead times. Robotic systems and CNC machines are widely used for precision machining, assembly, and inspection tasks.
3. Hot Runner
GETTING A QUOTE WITH LK-MOULD IS FREE AND SIMPLE.
FIND MORE OF OUR SERVICES:
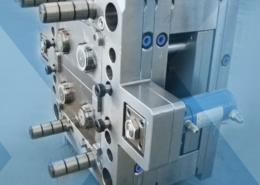
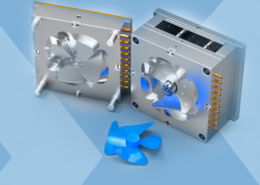
Plastic Molding
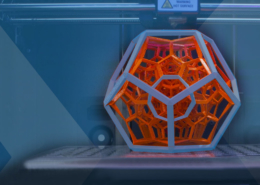
Rapid Prototyping
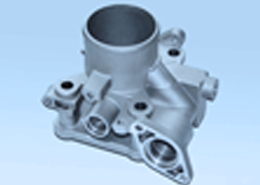
Pressure Die Casting
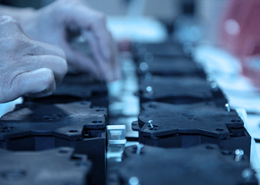
Parts Assembly
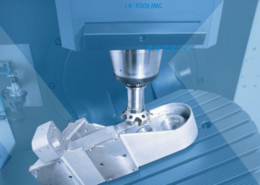