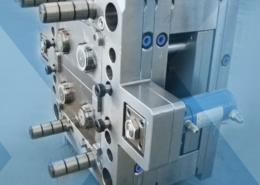
What is Plastic Overmolding? - plastic injection overmolding
Author:gly Date: 2024-10-15
We understand the importance of speed in bringing new products to market. Our quick-turn tooling services enable us to deliver parts within a month after placing an order. This rapid turnaround time allows you to accelerate your product development cycles and respond swiftly to market demands, giving you a competitive edge.
We have a defined project management and quality assurance process for intaking tools from other manufacturers. Our team can repair and modify existing tools to get your production back on track quickly. With our expertise, we ensure a smooth transition and minimal disruption to your manufacturing process.
We can handle parts with surface areas up to 156 square inches in the direction of the mold clamp. Specific dimensions like 10x15 or 12x13, and shot weights up to 61 ounces (3.8 pounds), are within our capacity.
Micro injection molding is a technique for producing tiny and precise components using minimal resin volumes in the injection procedure. Our expertise in micro injection molding allows us to create intricate parts with high accuracy, perfect for industries such as medical devices, electronics, and automotive components.
Beyond molding, we provide comprehensive post-processing and assembly services. Our secondary operations include machining, bonding, and finishing, ensuring that your parts are ready for immediate use. We can also offer assembly and packaging in our Class 8 Clean Room, maintaining the highest standards of cleanliness and quality.
Our injection molding services cater to a wide range of needs, from small quantity prototypes to full-scale production. Whether you need a few test pieces or millions of units, we have the capability to meet your demands efficiently. Our flexible production processes ensure that you receive high-quality parts on time, every time.
Our overmolding process allows us to combine multiple materials into a single component, enhancing functionality and performance. This process is ideal for creating ergonomic designs and improving the durability of parts. We use cutting-edge technology to ensure a seamless bond between materials, resulting in superior end products.
Design for Manufacturing (DFM) for injection molding involves optimizing the design of parts to improve manufacturability, reduce costs, and enhance quality. By integrating DFM principles, we ensure your designs are ready for efficient and effective injection molding production.
Minimize or eliminate undercuts to simplify mold design and reduce tooling costs. For instance, redesigning a part to avoid internal undercuts can eliminate the need for side actions in the mold.
Hot Tags: Plastic Automotive Air Conditioning Parts Injection Mold, China, factory, manufacturers, customized, made in China, Gas inject mould automotive parts deisgn, Gas inject mould for automotive parts, Mould For Auto Airbag Cover, Automotive mould, gas assist injection molding Automotive plastics, Automotive Parts Mould
Odin Mould(atplas) is a professional manufacture of gas-assisted injection mold, daily-use plastics mould, SMC/BMC mould, thin-wall injection mold, injection molding OEM,we have cultivated an excellent team and established a comprehensive system to meet different Different needs of customers.
The overmolding process enhances the functionality and aesthetics of a product by combining different materials, such as a rigid plastic with a soft-touch surface. Insert molding integrates metal or plastic inserts into the molded parts, increasing strength and functionality, and is ideal for creating complex assemblies.
We can work with a wide range of thermoplastic materials, including ABS, polycarbonate, polyethylene, polypropylene, and more. We select materials based on your specific application requirements, such as strength, flexibility, and temperature resistance. We do not work with PVC or Teflon.
We view our clients as partners and are dedicated to supporting your success from concept to completion. Our experienced team is available to assist with design, prototyping, production, and post-production services. This end-to-end support ensures a smooth and successful project execution, allowing you to focus on your core business objectives.
Our Design for Manufacturing (DFM) services help you optimize your designs for efficient and cost-effective production. By collaborating early in the design process, we identify potential issues and suggest improvements to enhance manufacturability. This proactive approach reduces time-to-market, lowers production costs, and ensures that your products are designed with manufacturing efficiency in mind.
We accept small batch custom molding services (Both thermoset and thermoform plastic). We CNC prototype, mold design, injection, silkscreen, engraver, assembly and packing as a whole.
Injection molding process for automobile air outlet Injection molding process for automobile air outlet.1. The air outlet mold should have the stability of injection production and the repeatability of process parameter adjustment within the range of normal injection molding process conditions.2. The injection pressure during mold injection production should generally be less than 85% of the rated maximum injection pressure of the injection molding machine.3. The injection speed during mold injection production, the injection speed of three quarters of its stroke is not lower than 10% of the rated maximum injection speed or exceeds 90% of the rated maximum injection speed.
For mold spare parts, such as springs, thimbles, hot runner accessories, etc., our company will provide customer maintenance and use free of charge.
Choose materials that are suitable for injection molding and meet your product's performance requirements. For instance, selecting a high-impact resin for a component that will experience significant wear and tear.
Optimize gate locations to ensure uniform filling and minimize defects. For example, placing the gate at the thickest section of a part helps ensure proper material flow and reduces the risk of sink marks.
Product Description 1.If you have 3D STEP/IGES/X_T drawing or 2D drawing, please directly send to us before quotation, then we will do mould design for you. 2.If you have samples no drawings, please directly provide us samples, we can design 3D for you,and quotation. Our Services -Reply...
Use ribs and gussets to add strength without increasing wall thickness. For example, adding ribs to a plastic panel increases rigidity while keeping the part lightweight.
At Aprios, we specialize in precision plastics for mission-critical parts, focusing on creating components where lives may be on the line, such as medical devices and safety equipment. We understand the gravity of plastic manufacturing for applications where failure is not an option, ensuring our plastic molding products meet the standards of accuracy, reliability, and performance. Our quality control processes and plastic molding techniques ensure that every part we produce is flawless, making us the ideal choice for high-stakes plastic manufacturing that requires dependability, rather than commodities like plastic spoons.
4. Generally, the holding pressure during injection molding of automobile air outlet mold should be less than 85% of the actual maximum injection pressure.5. The clamping force during mold injection production should be less than 90% of the rated clamping force of the applicable model.6. During the production process of injection molding, the products and nozzle materials should be easy and safe to take out (the time usually does not exceed 2 seconds each).7. For molds with inserts, the inserts should be easy to install and the inserts should be fixed reliably during production.
-Reply inquiry in 24 hours, sales team support on line.-Excellent enrich experience engineer team support on line.--100% inspection before shipment.--One-stop solution service (including die casting, cnc maching, silicone etc..)
We offer specialized medical molding services to produce high-precision, sterile components for the healthcare industry. Our Class 8 Clean Room ensures that all medical parts are manufactured in a controlled, contamination-free environment. This guarantees the highest standards of cleanliness and compliance with medical regulations.
Conduct mold flow analysis to predict and address potential issues such as air traps, weld lines, or hotspots. For example, simulating the injection process for a complex part can help optimize gate locations and cooling channels.
We adhere to strict quality control processes, including comprehensive testing and inspection at various stages of production. Our commitment to quality ensures that each part meets your exact specifications and industry standards.
Incorporate appropriate draft angles (typically 1-2 degrees) on vertical surfaces to facilitate easy ejection from the mold. For instance, adding a slight taper to the sides of a plastic cup makes it easier to remove from the mold.
Insert molding integrates metal or plastic inserts into the molded parts during the injection process. This technique enhances the strength and functionality of components, making it perfect for complex assemblies. Our expertise in insert molding allows us to produce parts with embedded reinforcements, electrical components, or threaded inserts with precision.
Maintain uniform wall thickness to prevent defects such as warping and sink marks. For example, designing a plastic enclosure with consistent wall thickness ensures even cooling and material flow.
By incorporating these considerations into your design, we ensure a more efficient injection molding process, leading to high-quality, cost-effective parts.
Yes, we have the capability to manage both small quantity prototypes and large-scale production runs. Our flexible manufacturing processes ensure high-quality production regardless of the order size.
We adhere to stringent quality assurance protocols and comply with industry standards to ensure the reliability of every part we produce. Our comprehensive testing and inspection processes guarantee that each component meets your exact specifications. For more information, please visit our Quality page. This commitment to quality reduces the risk of defects and enhances the overall performance of your products.
GETTING A QUOTE WITH LK-MOULD IS FREE AND SIMPLE.
FIND MORE OF OUR SERVICES:
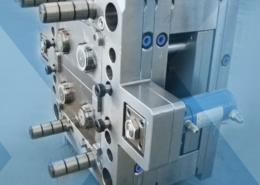
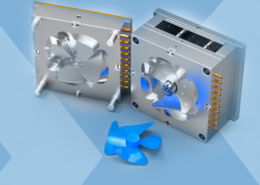
Plastic Molding
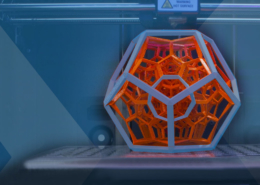
Rapid Prototyping
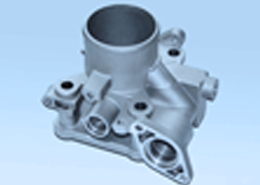
Pressure Die Casting
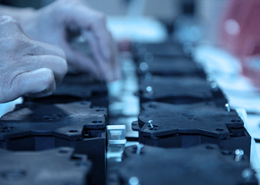
Parts Assembly
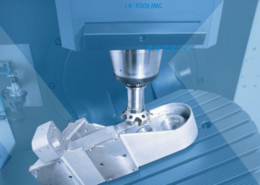