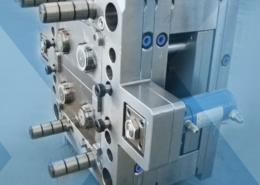
What to Consider for Injection Molding Polyethylene - polyethylene moulding
Author:gly Date: 2024-10-15
Composite molding uses a two-shot molding technology to add a layer of high performance composite material onto another molded element made from a more rigid plastic. The rigid component acts as a substrate for the composite material. The composite has expansion properties during the curing process, and, after cooling, the final component now has a thick layer of composite firmly affixed to the rigid substrate. Core-back molding has the capability to add more structural strength to components with little added weight, making it an ideal choice for many types of applications where this structural efficiency is desired. New products using core-back molding can also provide this greater strength at a reduced cost to the consumer.
Co-injection molding involves injection of two dissimilar materials. Because of this, co-injection has some special advantages, as well as some potential molding problems. The Co-injection analysis helps you overcome the potential problems and leverage the advantages, by helping to optimize process control strategies and enhance part quality.
Co-injection molding takes advantage of a characteristic of injection molding called fountain flow. As the cavity is filled, the plastic at the melt front moves from the center line of the stream to the cavity walls. Because the wall temperature is below the transition temperature (freeze temperature) of the melt, the material that touches the walls cools rapidly and freezes in place. This provides insulating layers on each wall, through which new melt makes its way to the melt front.
The skin plastic is the material that is expected to be deposited on the cavity wall over the entire surface of the part. The core plastic displaces the skin plastic at the hot core, pushing it to fill the rest of the cavity. The end product is a sandwich-like structure, with the core plastic in the middle and the skin plastic on the surfaces of the part.
Co-Injection analysis simulates the sequential injection of skin and core plastic materials. Sequential co-injection processes have two barrels and one nozzle in an injection molding machine.
(a) The skin plastic is injected into the mold first. (b) The core plastic then is injected. (c) finally, the skin plastic is injected again, to purge the core material from the sprue .
Plastic manufacturing and the evolution of thermoplastic injection molding technology has continued to develop with a range of innovative options that add potential savings and performance. Aline Components is a leading plastic injection molding company serving the Tri-State area with the finest plastic parts and employing the most advanced custom plastic injection molding equipment and expertise. Composite molding, also known as core-back molding, is a relatively recent thermoplastic injection molding technique that makes use of innovations in material science to enhance new products and components.
Aline Components serves customers in Pennsylvania, New Jersey, Delaware, New York, and beyond. Conveniently located just outside Philadelphia, its state-of-the-art facility employs the latest injection molding equipment and offers plastic parts with all of the most advanced features, such as insert molding, sandwich molding, stack molding for large production runs, and more. Alineâs services range from CAD/CAM documentation support, rapid prototyping, and short-run processes for rush delivery. If you are looking for experienced plastic injection molding company with a detailed knowledge of the most current plastic manufacturing techniques, including composite/core-back molding, contact Aline Components today.
At Aline Components, we work with you to determine if insert molding is right for your plastic part or component, and if so, what material is best suited for the application. We take pride in helping our customers obtain the solutions they need for their product or system to perform to the highest level.
GETTING A QUOTE WITH LK-MOULD IS FREE AND SIMPLE.
FIND MORE OF OUR SERVICES:
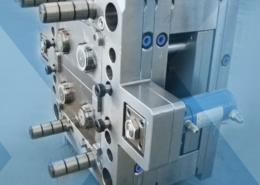
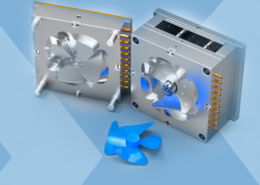
Plastic Molding
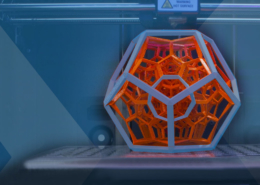
Rapid Prototyping
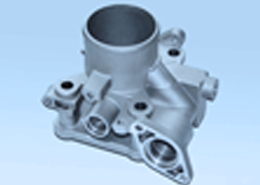
Pressure Die Casting
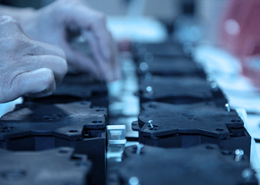
Parts Assembly
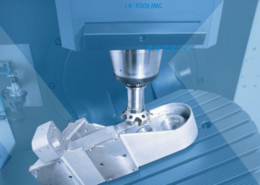