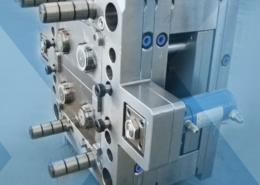
What's the difference between injection moulding and ... - extrusion and injecti
Author:gly Date: 2024-10-15
Yes, HDPE (High-Density Polyethylene) is widely used in injection molding applications. It is a versatile resin known for its high impact resistance, excellent stress crack resistance, and extreme durability, making it ideal for a variety of consumer and industrial products.
Cooling Rates: Rapid yet controlled cooling is essential to avoid warping or shrinkage while maintaining dimensional accuracy.
HDPE can be found in various items, including household containers, toys, industrial pipes, and heavy-duty shipping crates.
Yes, HDPE can be easily molded into a variety of shapes and sizes. Its smooth texture and uniform structure make it suitable for creating complex designs through injection molding, making it a popular material for both industrial and consumer products.
HDPE’s impact strength, measured using the Izod test, is quite high, making it resistant to sudden impacts or heavy pressure.
JavaScript seems to be disabled in your browser. For the best experience on our site, be sure to turn on Javascript in your browser.
It also performs well in low-temperature environments, maintaining its strength and durability even under cold conditions.
Its non-toxic, moisture-resistant, and chemical-resistant properties make HDPE a reliable material for products that must meet stringent health and safety standards.
Sink Marks: These depressions on the surface of molded parts are caused by inadequate cooling or high injection pressure. They occur when the material shrinks inward due to a lack of support from the surrounding mold.
Adjust Process Parameters: Increase the melt temperature and slow down the injection speed to reduce issues like voids and bubbles. This allows for better material flow and minimizes air entrapment within the mold.
When it comes to injection molding, HDPE (High-Density Polyethylene) offers distinct advantages, but it’s important to compare it to other common thermoplastics like polypropylene (PP) and nylon (PA) to understand its unique properties and best-use cases.
Proper mold design, with cooling channels positioned close to the mold surface, can help minimize these effects and produce parts with high precision.
Whether it’s used in heavy-duty industrial parts or everyday consumer goods, HDPE’s ability to maintain structural integrity under stress makes it a preferred material for injection molding.
Temperature Sensitivity: HDPE’s mechanical properties can change significantly at higher temperatures, making it less ideal for applications exposed to extreme heat.
This plastic also has exceptional chemical resistance, making it immune to damage from most acids, bases, and other harsh substances.
We are committed to helping you elevate quality standards, fostering enterprise growth, and actualizing your internationalization strategy.
Several key parameters need to be carefully controlled during the HDPE injection molding process to ensure optimal results:
Warping: Warping occurs when parts cool unevenly, leading to distortion. It is often a result of improper mold design or non-uniform cooling across the part.
Special attention should be given to shrinkage and warping during the cooling phase, as HDPE’s shrinkage rate can range from 1.5% to 4%.
Their sophisticated product portfolio of Secure Base URL">injection moulding machine construction covers the entire spectrum of the plastics processing industry and meets the most diverse customer demands for the manufacture of mass and high-precision plastic products.
Known for its strength, durability, and cost-effectiveness, HDPE has become a go-to material for injection molding applications.
Its tensile strength typically ranges from 3,200 to 4,500 psi, and its flexural modulus—measuring how much it can bend without breaking—falls between 145,000 to 225,000 psi.
Voids and Bubbles: Voids or air bubbles form when air gets trapped inside the material during the injection process. Fast injection speeds or improper venting can also contribute to this issue.
Its versatility allows manufacturers to mold HDPE into countless shapes and forms, making it popular in industries like packaging, automotive, construction, and more.
HITOP is committed to assisting customers by offering a comprehensive one-stop solution, encompassing product design enhancement, initial sample creation, mold fabrication, injection molding, and product assembly.
HDPE injection molding is a versatile, cost-effective solution for producing durable, high-quality plastic products across various industries.
HDPE’s chemical and moisture resistance also makes it suitable for construction hardware, where durability is required in harsh environments.
Mold Temperature: Mold temperatures should be kept between 20-95°C (68-194°F), depending on wall thickness. Thicker walls require higher mold temperatures to ensure uniform cooling.
High Shrinkage: HDPE’s relatively high shrinkage rate can affect the accuracy of designs, requiring extra consideration during the molding process to achieve precise results.
Optimize Mold Design: To prevent warping, ensure consistent wall thickness and proper cooling channel placement. Design considerations like uniformity in wall thickness can help in maintaining dimensional stability during cooling.
Additionally, HDPE is resistant to moisture, which makes it perfect for packaging products, piping systems, and even electrical insulation.
It begins with material selection, where the right grade of HDPE is chosen based on the desired properties and application.
Whether you’re using HDPE to manufacture sturdy automotive parts, everyday consumer goods, or reliable packaging solutions, this thermoplastic excels in offering top-notch performance across various industries.
FDA Approved: HDPE is available in FDA-approved grades, making it safe for food and medical applications, further increasing its versatility.
FDA-approved HDPE is used to manufacture medical-grade tubing, containers for food and pharmaceuticals, and even certain medical devices.
Barrel Temperature: HDPE melts at temperatures between 180-280°C (356-536°F), depending on the specific grade. Maintaining the right temperature ensures proper melting without degrading the material.
Injection Pressure: Typical pressures range from 70 to 105 MPa, depending on the part’s size and complexity. This pressure ensures the molten HDPE fully fills the mold without defects.
Hi, I am Sparrow Xiang, COO of the HiTop company, me and my team would be happy to meet you and learn all about your business, requirements and expectations.
Its strength, lightweight nature, and resistance to moisture and chemicals allow it to handle tough conditions, making it a preferred choice in everything from food packaging to construction.
Difficult to Bond: Due to its low surface energy, HDPE can be challenging to bond with other materials, often requiring specialized adhesives or surface treatments.
The material’s versatility ensures it meets the demanding needs of industrial applications, from automotive to heavy-duty packaging.
Chemical and Moisture Resistance: HDPE’s ability to resist chemicals and moisture makes it ideal for outdoor and industrial applications where exposure to harsh environments is common.
HDPE injection molding is primarily used in industrial, automotive, and consumer goods applications. It can also be used for specialized products such as FDA-approved grades for food contact and medical devices, although these applications are less common.
Durable: With a high strength-to-density ratio, HDPE is incredibly resilient, making it suitable for products that require toughness and longevity.
The HDPE injection molding process involves several critical steps that transform raw HDPE pellets into a finished part.
The melt temperature of HDPE for injection molding typically ranges from 180-280°C. For high molecular weight HDPE grades, the ideal melting temperature range is slightly narrower, from 200-250°C. The mold temperature usually ranges between 20-95°C.
The HDPE injection molding process begins by melting the HDPE pellets until they reach a moldable state. Once the material reaches the appropriate temperature inside the injection molding machine, it is injected into a mold cavity made of two parts—referred to as the “A” and “B” sides. After filling the cavity, the material hardens and cools into the desired shape almost immediately.
Control Injection Pressure: To avoid sink marks, fine-tune the injection pressure and ensure adequate cooling time. Balancing these factors helps achieve a smoother surface and reduces the likelihood of defects.
Haitian has a solid foundation to take care of what customers really need. They have been sustainably developing their service team and service skills from learning from the past and accumulation of practical experience. They have a well-trained after-sales service team with excellent technical qualification and profound practical experience.
Its strength, chemical resistance, and recyclability make it an ideal choice for applications ranging from consumer goods to industrial components.
Flow Marks: Flow marks are visible streaks or lines that occur on the surface of the part. These are typically caused by low melt temperatures or inconsistent material flow within the mold cavity.
Recyclable: Eco-friendly and fully recyclable, HDPE plays a role in reducing waste and supporting sustainable manufacturing practices.
Additionally, household items such as milk crates, laundry baskets, and appliance components are often made from HDPE due to their strength and resistance to impact.
HDPE’s adaptability across many industries comes from its excellent ability to balance strength, durability, and affordability.
Cost-effective: HDPE is an affordable material, making it a go-to option for manufacturers across various industries due to its cost efficiency.
GETTING A QUOTE WITH LK-MOULD IS FREE AND SIMPLE.
FIND MORE OF OUR SERVICES:
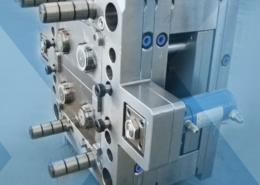
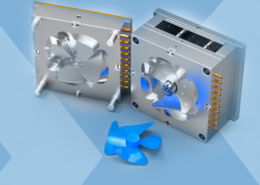
Plastic Molding
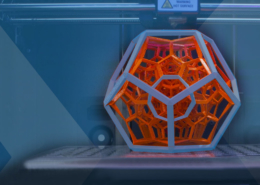
Rapid Prototyping
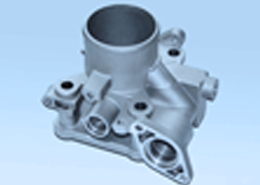
Pressure Die Casting
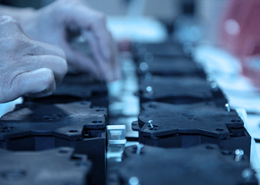
Parts Assembly
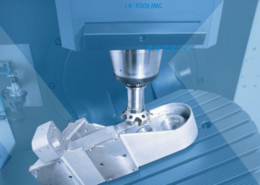