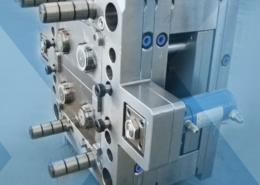
Exploring Prototype Plastic Injection Molding: Revolutionizing Product Developme
Author:gly Date: 2024-06-08
Introduction
Prototype plastic injection molding stands at the forefront of modern manufacturing, revolutionizing the way products are conceptualized, designed, and brought to market. In this article, we delve into the intricate world of prototype plastic injection molding, unraveling its significance, applications, challenges, and future prospects.
Background
Plastic injection molding is a manufacturing process wherein molten plastic is injected into a mold cavity under high pressure, cooled, and solidified to produce a desired component. Prototyping within this realm involves creating preliminary models or samples of a product to test its design, functionality, and manufacturability before mass production. This iterative process is crucial in mitigating risks, reducing costs, and accelerating time-to-market for new products.
Applications
Automotive Industry
Prototype plastic injection molding plays a pivotal role in the automotive sector, facilitating the development of vehicle components ranging from interior trims to complex engine parts. By enabling rapid prototyping of various designs and materials, manufacturers can efficiently evaluate performance, durability, and aesthetic appeal.
Consumer Electronics
In the fast-paced world of consumer electronics, speed to market is paramount. Prototype plastic injection molding empowers companies to swiftly iterate designs for smartphones, laptops, wearables, and other gadgets, ensuring optimal functionality and user experience.
Medical Devices
In the healthcare domain, precision and reliability are non-negotiable. Prototyping with plastic injection molding allows medical device manufacturers to test prototypes for accuracy, biocompatibility, and regulatory compliance, paving the way for innovative solutions in diagnostics, treatment, and patient care.
Technological Advances
3D Printing Integration
The integration of 3D printing technologies with prototype plastic injection molding has revolutionized the prototyping process. By leveraging additive manufacturing techniques, engineers can rapidly produce intricate molds with unprecedented speed and precision, opening new frontiers in design freedom and customization.
Material Innovations
Advancements in polymer science have expanded the repertoire of materials available for prototype plastic injection molding. From traditional thermoplastics to high-performance engineering resins, the diverse material options cater to a wide spectrum of applications, spanning from lightweight consumer products to high-temperature industrial components.
Digital Twin Simulation
The advent of digital twin simulation software has streamlined the prototyping workflow, allowing engineers to simulate the injection molding process virtually. By analyzing factors such as flow dynamics, cooling rates, and part shrinkage, manufacturers can optimize mold designs and processing parameters, minimizing defects and enhancing efficiency.
Challenges and Considerations
Design Complexity
Complex geometries and intricate features pose challenges in prototype plastic injection molding, necessitating careful design considerations to ensure moldability, part quality, and dimensional accuracy. Collaborative efforts between designers, engineers, and molders are essential to overcome these challenges effectively.
Cost Constraints
While prototype plastic injection molding offers unparalleled benefits in terms of speed and flexibility, cost considerations remain a critical factor, particularly for small-scale productions and startups. Balancing the trade-offs between prototyping expenses and potential savings in downstream manufacturing is essential for maximizing return on investment.
Material Selection
Selecting the appropriate material for prototyping is a nuanced decision influenced by factors such as mechanical properties, surface finish, and cost-effectiveness. Conducting thorough material characterization and performance testing is imperative to ensure that prototypes accurately represent the intended end-use conditions.
Conclusion
Prototype plastic injection molding stands as a cornerstone of modern product development, empowering innovators to iterate, validate, and refine designs with unprecedented efficiency and precision. By harnessing technological advancements, addressing key challenges, and embracing a collaborative mindset, manufacturers can unlock new frontiers of innovation and drive sustainable growth in the ever-evolving landscape of manufacturing.
In conclusion, the continued advancement of prototype plastic injection molding holds immense promise in accelerating product innovation, enhancing competitiveness, and meeting the evolving needs of consumers and industries worldwide. As we navigate the complexities of a rapidly changing world, investing in research, education, and cross-disciplinary collaboration will be essential in shaping the future trajectory of this transformative technology.
GETTING A QUOTE WITH LK-MOULD IS FREE AND SIMPLE.
FIND MORE OF OUR SERVICES:
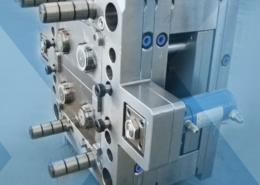
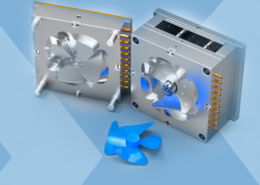
Plastic Molding
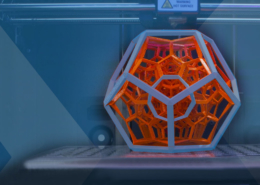
Rapid Prototyping
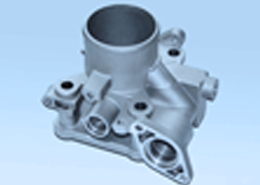
Pressure Die Casting
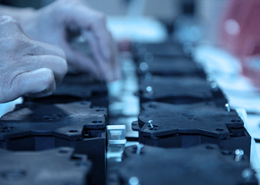
Parts Assembly
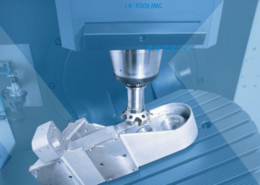