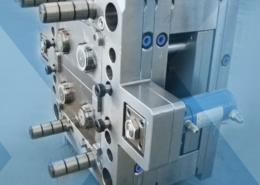
Unveiling the Power of Scientific Molding
Author:gly Date: 2024-06-08
Scientific molding represents a pinnacle in the art and science of injection molding. This article aims to unravel the complexities of scientific molding, offering insights into its significance, principles, applications, and future directions.
Introduction
Scientific molding is not just a manufacturing technique; it's a philosophy that emphasizes precision, optimization, and data-driven decision-making in the injection molding process. Unlike traditional molding approaches, which rely on trial and error, scientific molding leverages empirical data, mathematical models, and advanced technology to achieve superior results. This methodology has revolutionized the way injection molding is performed, elevating it to a realm of scientific rigor and predictability.
Principles of Scientific Molding
At the heart of scientific molding lies a set of fundamental principles that govern the entire molding process, from material selection to tool design to process optimization.
Material Characterization and Selection
Scientific molding begins with a thorough understanding of the material properties and behavior. Manufacturers conduct comprehensive material characterization studies to determine key parameters such as melt flow, viscosity, shrinkage, and thermal stability. This data-driven approach enables informed decisions regarding material selection, ensuring compatibility with the intended application and processing conditions.
Process Optimization and Control
Central to scientific molding is the concept of process optimization and control. Through systematic experimentation and statistical analysis, manufacturers identify optimal process parameters that yield consistent, high-quality parts. Advanced molding technologies, such as closed-loop control systems and real-time monitoring devices, enable precise adjustment of key variables such as temperature, pressure, and injection speed, ensuring reproducibility and repeatability in production.
Mold Design and Simulation
Another critical aspect of scientific molding is mold design and simulation. Utilizing advanced CAD/CAM software and finite element analysis (FEA) tools, engineers can simulate the mold filling process, predict potential defects, and optimize mold geometry for uniform cavity filling and part quality. By integrating simulation-driven design principles into the mold development process, manufacturers can reduce lead times, minimize tooling costs, and optimize part performance.
Applications of Scientific Molding
The applications of scientific molding span across various industries, including automotive, medical, consumer electronics, and aerospace. Its precision, consistency, and efficiency make it the preferred choice for manufacturing complex, high-performance components.
Automotive Industry
In the automotive industry, where stringent quality standards and tight tolerances are paramount, scientific molding plays a critical role in producing structural components, interior trim, and exterior body panels. By achieving uniform material distribution, minimal warpage, and dimensional stability, scientific molding enables automakers to enhance vehicle safety, performance, and aesthetics.
Medical Devices
In the medical device industry, where product reliability and biocompatibility are non-negotiable, scientific molding ensures the precise fabrication of components such as syringes, IV connectors, and surgical instruments. By adhering to strict process controls and regulatory requirements, manufacturers can produce medical-grade parts with exceptional consistency and cleanliness, meeting the demands of healthcare professionals and patients alike.
Consumer Electronics
In the realm of consumer electronics, where design aesthetics and functional integration are paramount, scientific molding enables the production of sleek, lightweight, and durable components such as smartphone cases, laptop enclosures, and electronic housings. By leveraging advanced materials and molding techniques, manufacturers can achieve intricate designs, tight tolerances, and superior surface finishes, delivering products that resonate with consumers' preferences and lifestyles.
Advancements and Future Directions
As technology continues to evolve and market demands evolve, the field of scientific molding is poised for further advancements and innovations.
Advanced Materials and Additive Manufacturing
The emergence of advanced materials, such as bioplastics, composites, and nanomaterials, presents new opportunities and challenges for scientific molding. By incorporating these materials into the molding process and leveraging additive manufacturing techniques, manufacturers can unlock new design possibilities, enhance material properties, and reduce environmental impact.
Digital Twin and Industry 4.0 Integration
The integration of digital twin technology and Industry 4.0 principles promises to revolutionize scientific molding. By creating virtual replicas of the molding process and leveraging real-time data analytics, manufacturers can optimize process parameters, predict equipment failures, and achieve continuous improvement in quality and efficiency. This digital transformation will pave the way for smart, connected, and autonomous manufacturing systems, driving unprecedented levels of productivity and innovation.
Conclusion
In conclusion, scientific molding represents a paradigm shift in the field of injection molding, blending art with science to achieve unparalleled levels of precision, efficiency, and quality. Its principles and methodologies have redefined the way manufacturers approach the molding process, setting new standards for performance and reliability. As technology continues to advance and market demands evolve, the future of scientific molding looks brighter than ever, with endless possibilities for innovation and growth. Embracing these advancements and leveraging them to their fullest potential will be essential for manufacturers to stay ahead of the curve and maintain a competitive edge in the dynamic world of manufacturing.
GETTING A QUOTE WITH LK-MOULD IS FREE AND SIMPLE.
FIND MORE OF OUR SERVICES:
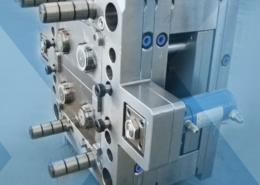
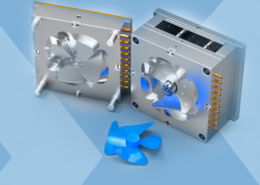
Plastic Molding
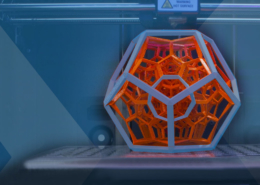
Rapid Prototyping
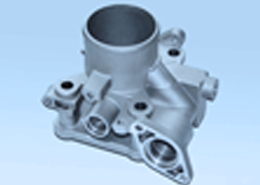
Pressure Die Casting
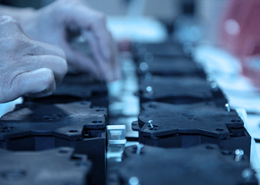
Parts Assembly
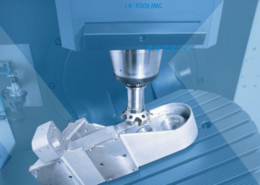